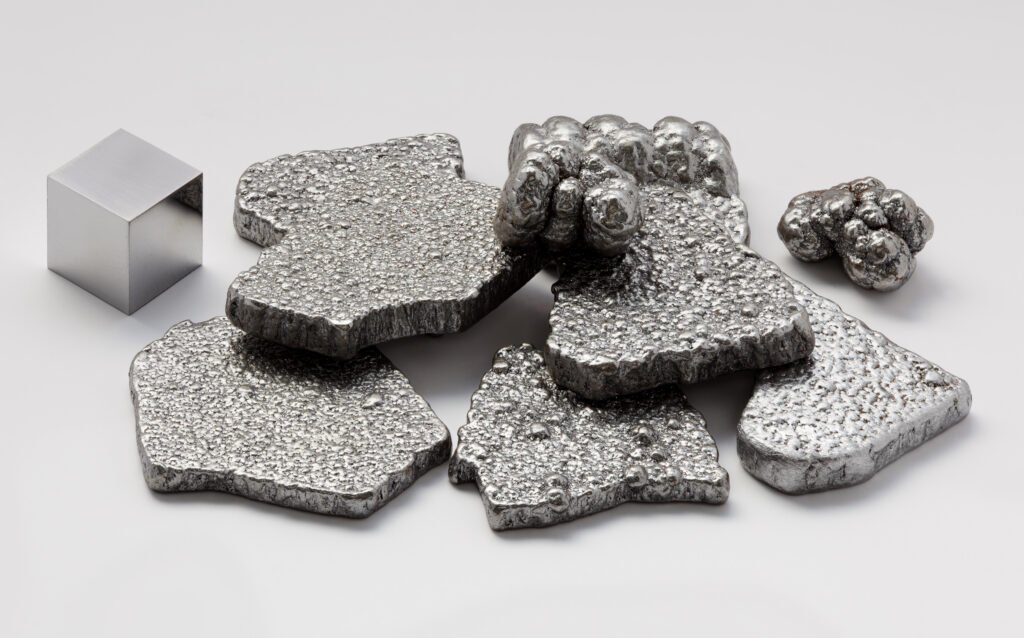
Da Mineralogia ao Aço: A Jornada dos Minerais até as Aplicações na Indústria
A matéria-prima que alimenta a engrenagem industrial moderna tem origem nas profundezas da Terra. Minerais, muitas vezes despercebidos sob nossos pés, percorrem um longo caminho até se transformarem em materiais fundamentais como o aço. Este texto traça essa fascinante jornada: da formação mineralógica ao protagonismo industrial.
O Berço dos Minerais: Mineralogia e Geologia como Bases da Indústria Siderúrgica
A produção de aço, elemento essencial da infraestrutura e tecnologia modernas, depende da extração e transformação de minerais metálicos específicos, principalmente o ferro. Este artigo explora os fundamentos da mineralogia e da geologia na formação, caracterização e exploração dos principais minerais de ferro, com destaque para hematita, magnetita e pirita. São discutidos os processos geológicos responsáveis pela origem desses minerais, suas propriedades físico-químicas e os métodos de prospecção e extração mineral empregados na indústria siderúrgica.
Palavras-chave: mineralogia, geologia, hematita, magnetita, siderurgia, mineração.
1. Introdução
A cadeia produtiva do aço tem início muito antes das siderúrgicas, nos domínios da geologia e da mineralogia. É nesses campos que se estabelece o conhecimento sobre a origem, composição e distribuição dos minerais metálicos. Dentre eles, os minerais de ferro destacam-se pela importância econômica e tecnológica, sendo a base da indústria siderúrgica global (DNPM, 2019).
A compreensão dos processos geológicos que levam à formação desses minerais, bem como as técnicas de prospecção e extração, é fundamental para a exploração eficiente e sustentável dos recursos naturais.
2. Fundamentos da Mineralogia e da Geologia
A mineralogia é a ciência que estuda os minerais quanto à sua composição química, estrutura cristalina, propriedades físicas e condições de formação. Enquanto isso, a geologia fornece o arcabouço teórico e prático para entender os processos geodinâmicos que resultam na concentração natural desses minerais em depósitos economicamente viáveis (KLEIN; DUTROW, 2012).
Segundo Klein e Dutrow (2012), um mineral é uma substância sólida, inorgânica, com composição química definida e estrutura interna ordenada. A maioria dos minerais de interesse econômico se origina a partir de três grandes processos geológicos: magmáticos, metamórficos e sedimentares.
3. Formação dos Minerais: Processos Geológicos
3.1 Processos Magmáticos
Minerais formados a partir do resfriamento e solidificação do magma, como a magnetita (Fe₃O₄), estão comumente associados a rochas ígneas intrusivas e são frequentemente encontrados em ambientes geotectônicos específicos, como complexos máficos-ultramáficos (ROBERTS; NESBITT, 2002).
3.2 Processos Metamórficos
O metamorfismo atua na transformação mineralógica e estrutural de rochas preexistentes sob condições de alta pressão e temperatura. A hematita (Fe₂O₃) pode se formar em ambientes metamórficos, principalmente por recristalização de depósitos ferruginosos sedimentares (STACEY; BANERJEE, 1974).
3.3 Processos Sedimentares
Formações ferríferas bandadas (Banded Iron Formations – BIFs) são depósitos sedimentares originados em ambientes marinhos precambrianos, ricos em hematita e goethita, e representam as maiores jazidas de ferro do mundo, como no Quadrilátero Ferrífero, Brasil (MARTINS et al., 2011).
4. Minerais Metálicos de Interesse Siderúrgico
4.1 Hematita (Fe₂O₃)
- Teor de ferro: até 70%.
- Formação: predominantemente sedimentar e metamórfica.
- Importância: principal minério de ferro utilizado na indústria siderúrgica devido à sua alta concentração e facilidade de beneficiamento (DNPM, 2019).
4.2 Magnetita (Fe₃O₄)
- Teor de ferro: até 72%.
- Formação: magmática ou metamórfica.
- Particularidade: possui propriedades magnéticas e requer maior complexidade na separação e redução (ROBERTS; NESBITT, 2002).
4.3 Pirita (FeS₂)
- Teor de ferro: cerca de 46%, porém não é utilizada como fonte primária de ferro.
- Utilização: fonte de enxofre para produção de ácido sulfúrico; apresenta riscos ambientais por gerar drenagem ácida (MORIN; HUTCHINSON, 2000).
5. Prospecção, Mapeamento e Extração Mineral
A identificação e aproveitamento de jazidas minerais envolvem múltiplas etapas técnicas e científicas:
5.1 Prospecção Mineral
Envolve o uso de métodos geofísicos, geoquímicos e sensoriamento remoto para identificar áreas com potencial mineral. Técnicas modernas incluem aerolevantamentos e uso de imagens hiperespectrais (REIS et al., 2020).
5.2 Mapeamento Geológico
Fundamental para entender a geologia regional e estrutural, o mapeamento permite prever a extensão dos depósitos e planejar economicamente a lavra (CPRM, 2016).
5.3 Sondagem e Lavra
A sondagem fornece amostras do subsolo, permitindo a modelagem geológica e cálculo de reservas. A lavra pode ser a céu aberto (como no caso das minas de hematita em Minas Gerais) ou subterrânea, dependendo das condições geotécnicas e econômicas.
6. Considerações
A formação e exploração dos minerais de ferro são resultado da interação complexa entre processos naturais e tecnologias humanas. A compreensão mineralógica e geológica desses recursos é essencial para garantir sua utilização racional, eficiente e ambientalmente sustentável. O estudo sistemático dos minerais, desde sua origem até a aplicação industrial, é uma das chaves para o desenvolvimento tecnológico e econômico contemporâneo.
Referências
- CPRM – Serviço Geológico do Brasil. Mapeamento geológico e recursos minerais do Brasil. Brasília: CPRM, 2016.
- DNPM – Departamento Nacional de Produção Mineral. Sumário Mineral Brasileiro. Brasília: DNPM, 2019.
- KLEIN, C.; DUTROW, B. Manual of Mineral Science. 23rd ed. Hoboken: Wiley, 2012.
- MARTINS, M. S.; DANTAS, E. L.; ANGÉLICA, R. S. et al. Geologia das Formações Ferríferas Bandadas do Quadrilátero Ferrífero. Revista Brasileira de Geociências, v. 41, n. 2, p. 191-206, 2011.
- MORIN, K.A.; HUTCHINSON, D.J. Acid Drainage from Mines: A Global Perspective. Vancouver: MDAG Publishing, 2000.
- REIS, L. D.; RODRIGUES, F. C.; OLIVEIRA, A. B. S. Sensoriamento remoto aplicado à prospecção mineral. Revista Geociências, v. 39, n. 3, p. 303-312, 2020.
- ROBERTS, W. L.; NESBITT, B. E. Geochemistry of Iron Oxide Deposits. Economic Geology, v. 97, n. 6, p. 1231-1248, 2002.
- STACEY, J. S.; BANERJEE, A. Geological Environments of Iron Ore Deposits. Mineralogical Magazine, v. 39, p. 781–792, 1974.
Da Mina à Usina: Extração e Beneficiamento de Minerais na Indústria Siderúrgica
A transformação de recursos minerais em insumos industriais depende de uma série de etapas que se iniciam com a extração do minério e seguem com o beneficiamento, processo crucial para o aproveitamento eficiente da matéria-prima. Este artigo explora as principais fases da cadeia mineral, desde os métodos de lavra até as técnicas de concentração mineral, como trituração, moagem e separação magnética. Também são discutidos os impactos ambientais da mineração e as estratégias de sustentabilidade aplicadas ao setor.
Palavras-chave: extração mineral, beneficiamento, mineração sustentável, separação magnética, trituração.
1. Introdução
A indústria mineral constitui a base da economia industrial moderna. No contexto siderúrgico, a produção de aço depende da transformação de minerais de ferro extraídos e processados adequadamente. O percurso entre a jazida mineral e a usina siderúrgica envolve etapas fundamentais: extração, beneficiamento e transporte. Cada uma dessas fases requer conhecimentos técnicos específicos, bem como planejamento voltado à redução de impactos ambientais e à eficiência energética (DNPM, 2019; VALE, 2020).
2. Métodos de Extração Mineral
2.1 Mineração a Céu Aberto
A lavra a céu aberto é o método mais comum para minérios com ocorrência superficial e em grandes volumes, como os depósitos ferríferos do Quadrilátero Ferrífero, em Minas Gerais. Esse método envolve a remoção do material estéril para acesso ao minério, utilizando escavadeiras, caminhões fora-de-estrada e explosivos (CALLIGARIS et al., 2015).
Vantagens:
- Menor custo operacional por tonelada.
- Maior produtividade.
- Facilitação da mecanização e automação.
Desvantagens:
- Maior impacto paisagístico.
- Geração de grandes volumes de resíduos (estéreis).
2.2 Mineração Subterrânea
Empregada quando os depósitos estão em profundidades superiores a 100 metros ou quando há restrições ambientais ou urbanas. A lavra subterrânea utiliza galerias, túneis e sistemas de ventilação. Embora mais dispendiosa, causa menor impacto visual e permite maior controle ambiental local (SOUZA, 2018).
3. Beneficiamento de Minérios
O beneficiamento mineral visa preparar o minério para utilização industrial, aumentando sua concentração e removendo impurezas. O processo é composto por diversas etapas sequenciais:
3.1 Trituração
Consiste na fragmentação grosseira do minério, geralmente realizada em britadores de mandíbula ou giratórios. Essa fase visa reduzir o tamanho das partículas para facilitar a moagem subsequente (CHAVES, 2012).
3.2 Moagem
Responsável por reduzir ainda mais o tamanho das partículas, a moagem é feita em moinhos de bolas ou de barras. É nessa fase que o minério atinge uma granulometria ideal para a separação físico-química (CHAVES, 2012).
3.3 Classificação Granulométrica
Utiliza peneiras vibratórias ou hidrociclones para separar o material moído por tamanho. Essa separação permite direcionar as partículas às etapas adequadas de concentração, aumentando a eficiência do processo.
3.4 Separação Magnética
Especialmente útil para minérios de ferro, a separação magnética baseia-se na diferença de suscetibilidade magnética entre os minerais. Minerais como hematita (Fe₂O₃) e magnetita (Fe₃O₄) respondem bem a essa técnica, especialmente quando em partículas finas (LOPES, 2019).
Tipos:
- Separação magnética de baixa intensidade (LIMS): para magnetita.
- Separação de alta intensidade (WHIMS): usada para hematita e outros minerais fracamente magnéticos.
4. Aspectos Ambientais e Sustentabilidade
A atividade mineradora impõe desafios ambientais relevantes, como degradação do solo, consumo excessivo de água e energia, geração de resíduos e riscos de acidentes com barragens de rejeito. Em resposta, o setor tem adotado práticas de mineração sustentável.
4.1 Gestão de Resíduos
O reaproveitamento de rejeitos, como no uso de “pellets” de minério fino, ou a disposição seca dos rejeitos, vem ganhando espaço como alternativa às barragens convencionais (ICMM, 2021).
4.2 Reabilitação de Áreas Degradadas
Planos de fechamento de mina e reabilitação ambiental são exigências legais em diversos países. Incluem reflorestamento, monitoramento de qualidade da água e reintegração ecológica das áreas mineradas (SOUZA; COSTA, 2017).
4.3 Eficiência Energética e Hídrica
O uso de tecnologias mais limpas, como flotação com reagentes biodegradáveis e sistemas de recirculação de água, contribui para a redução do impacto ambiental do beneficiamento mineral (IBRAM, 2020).
5. Considerações
O percurso que leva os minérios da mina à usina siderúrgica é complexo e demanda conhecimento técnico, gestão ambiental e eficiência operacional. A mineração moderna precisa conciliar produtividade com responsabilidade socioambiental, o que exige investimento constante em inovação e governança. O beneficiamento, ao permitir maior aproveitamento do recurso extraído, é peça-chave nesse processo.
Referências
- CALLIGARIS, G. A. et al. Lavra a céu aberto: fundamentos e aplicações. Revista Escola de Minas, v. 68, n. 4, p. 411-421, 2015.
- CHAVES, A. P. Mineralogia e técnicas de beneficiamento. São Paulo: Oficina de Textos, 2012.
- DNPM – Departamento Nacional de Produção Mineral. Sumário Mineral Brasileiro. Brasília: DNPM, 2019.
- IBRAM – Instituto Brasileiro de Mineração. Relatório de Sustentabilidade da Mineração Brasileira. Brasília: IBRAM, 2020.
- ICMM – International Council on Mining and Metals. Tailings Management: Good Practice Guide. Londres, 2021.
- LOPES, A. E. Técnicas de separação magnética aplicadas à indústria mineral. Boletim Técnico da Mineração, v. 44, n. 2, p. 33-49, 2019.
- SOUZA, M. T. Mineração Subterrânea no Brasil: desafios e oportunidades. Revista Minérios & Minerales, v. 59, n. 6, p. 42-47, 2018.
- SOUZA, R. M.; COSTA, H. F. Gestão ambiental em áreas mineradas: diretrizes para reabilitação. Revista de Geociências Ambientais, v. 25, n. 1, p. 89-98, 2017.
- VALE S.A. Relatório de Sustentabilidade 2020. Rio de Janeiro: VALE, 2020.
A Metalurgia: Transformando Minério em Metal
A metalurgia extrativa representa a etapa fundamental na transformação do minério de ferro em produtos metálicos utilizáveis, como o aço. Este artigo analisa, em profundidade, os processos metalúrgicos envolvidos desde a preparação da carga até o lingotamento contínuo, com ênfase no papel da coqueria, sinterização, altos-fornos, aciaria, forno panela, forno de arco elétrico, refino secundário, reciclagem e laminação. O enfoque está na integração tecnológica entre as etapas e nos avanços que promovem eficiência e sustentabilidade na siderurgia moderna.
Palavras-chave: metalurgia extrativa, ferro-gusa, aço, altos-fornos, aciaria, lingotamento, forno panela.
1. Introdução
A siderurgia moderna constitui uma das bases estruturais da economia global, fornecendo materiais essenciais à construção civil, automotiva, naval, energia e infraestrutura urbana. O núcleo desse sistema produtivo reside na metalurgia extrativa, ciência e técnica voltada à obtenção de metais a partir de seus minérios (GUPTA; KRISHNAMOORTHY, 2006). No caso do ferro, a rota mais difundida é a redução em altos-fornos, seguida pelo processamento em aciarias. O processo envolve diversas etapas, da preparação da matéria-prima à obtenção do aço final.
2. Preparação das Matérias-primas
2.1 Coqueria
A coqueria é a unidade industrial onde o carvão mineral é submetido a um processo de destilação seca a cerca de 1000–1100 °C, na ausência de oxigênio, formando o carvão coque, essencial como agente redutor e combustível nos altos-fornos (SANTOS et al., 2017).
Funções do coque:
- Fornecer calor para as reações de redução.
- Criar permeabilidade na carga do alto-forno.
- Atuar como agente redutor do óxido de ferro.
2.2 Sinterização
A sinteria promove a aglomeração de finos de minério de ferro, fundentes (como calcário e dolomita) e retornos da planta (pó de aciaria e escória), formando o sínter, que melhora a permeabilidade e regularidade da carga no alto-forno (NARASIMHAN, 2015).
3. Redução do Minério: Produção do Ferro-Gusa
O alto-forno é uma unidade vertical onde ocorre a redução dos óxidos de ferro a ferro metálico por meio do gás monóxido de carbono (CO), gerado pela combustão do coque.
3.1 Reações principais
- Fe₂O₃ + 3CO → 2Fe + 3CO₂
- C + O₂ → CO₂ → CO (com calor)
3.2 Produtos
- Ferro-gusa: liga de ferro com 3,5–4,5% de carbono, além de silício, manganês e fósforo.
- Escória: formada por impurezas fundidas removidas com adição de cal (CaO).
- Gás de alto-forno: reaproveitado para aquecimento de regeneradores ou geração de energia.
Tempo médio de residência do minério no alto-forno: 6–8 horas (POTTER; WILKINSON, 2009).
4. Aciaria: Conversão do Gusa em Aço
Na aciaria, o ferro-gusa líquido é convertido em aço por meio da remoção de carbono e outras impurezas, geralmente com a injeção de oxigênio.
4.1 Conversores LD (Linz-Donawitz)
O processo LD utiliza um jato de oxigênio puro (99,5%) insuflado sobre o gusa. A oxidação do carbono gera calor e reduz o teor de C a níveis desejáveis (0,02–2%).
Componentes adicionados:
- Cal viva (CaO): remove silício e fósforo.
- Sucata metálica: controla a temperatura e reutiliza resíduos.
4.2 Forno Panela (Ladle Furnace)
Usado para o refino secundário, ajusta-se a composição química e temperatura do aço. Permite desgaseificação (remoção de H, N), adições de elementos de liga e homogeneização.
5. Rotas Alternativas e Reciclagem
5.1 Forno Elétrico a Arco (EAF)
Fundamental para rotas de reciclagem, o forno de arco elétrico funde sucata metálica com arcos elétricos (~3500 °C) entre eletrodos de grafite. É mais flexível quanto à matéria-prima e energeticamente intensivo (MASAKI, 2014).
5.2 Refino Secundário
Após o forno elétrico ou o conversor, o aço líquido pode passar por etapas como:
- VOD (vacuum oxygen decarburization): remoção de carbono sob vácuo.
- RH (Ruhrstahl-Heraeus): desgaseificação sob vácuo com circulação.
6. Lingotamento Contínuo e Laminação
6.1 Lingotamento Contínuo
Transforma o aço líquido em semiacabados (tarugos, blocos, placas). O aço é vertido em moldes refrigerados, solidificando-se progressivamente em processo contínuo. Reduz perdas, aumenta a produtividade e melhora a qualidade do produto final (HABASHI, 1997).
6.2 Laminação
Os semiacabados passam por laminação a quente ou a frio, produzindo chapas, vergalhões, perfis ou bobinas.
- Laminação a quente: acima de 1100 °C.
- Laminação a frio: abaixo do ponto de recristalização; melhora acabamento e resistência mecânica.
7. Considerações Ambientais e Sustentabilidade
A siderurgia é intensiva em energia e emissões. Medidas como:
- Recirculação de gases de processo (alto-forno, aciaria),
- Uso de biomassa no lugar de coque,
- Reutilização de escória e pó de aciaria, são fundamentais para mitigar os impactos ambientais (WORLD STEEL ASSOCIATION, 2022).
8. Considerações
A metalurgia do ferro e do aço envolve uma sequência altamente coordenada de operações fisicoquímicas, térmicas e mecânicas. A compreensão detalhada de cada etapa — da coqueria ao lingotamento — permite não apenas a otimização da produção, mas também avanços em eficiência energética, redução de emissões e aumento da qualidade metalúrgica do produto final.
Referências
- GUPTA, R. C.; KRISHNAMOORTHY, N. Introduction to Iron and Steelmaking. Delhi: Prentice-Hall, 2006.
- HABASHI, F. Principles of Extractive Metallurgy. London: Gordon & Breach, 1997.
- MASAKI, H. Recent Trends in Electric Arc Furnace Technology. Ironmaking and Steelmaking, v. 41, n. 2, p. 145-151, 2014.
- NARASIMHAN, K. S. Agglomeration Processes in Ironmaking. Oxford: Elsevier, 2015.
- POTTER, R. A.; WILKINSON, B. The Blast Furnace Process. Cambridge: Cambridge Steelworks Press, 2009.
- SANTOS, M. C. et al. Tecnologia da Coqueria e Impactos Ambientais. Revista Tecnológica da Indústria Siderúrgica, v. 24, p. 58-67, 2017.
- WORLD STEEL ASSOCIATION. Sustainable Steel – Indicators 2022 and Trends. Brussels: worldsteel, 2022.
Aços e Suas Ligas: Versatilidade na Indústria
O aço é uma liga metálica fundamental para o desenvolvimento industrial, caracterizada principalmente pela combinação de ferro e carbono, podendo incorporar outros elementos de liga para modificar suas propriedades físico-químicas. Este artigo apresenta uma análise aprofundada das diferentes classes de aços, seus tratamentos térmicos, processos de endurecimento, além da normatização técnica, incluindo a classificação SAE/AISI. Também são discutidas as novas abordagens voltadas à sustentabilidade, como o conceito de “aço verde” e as práticas pós-produção.
Palavras-chave: aço, ligas metálicas, classificação SAE, tratamento térmico, aço verde, padronização.
1. Introdução
O aço é uma das ligas metálicas mais versáteis e amplamente utilizadas no mundo industrial moderno. Sua aplicação abrange setores como construção civil, automotivo, energia, ferroviário, naval e aeroespacial. Essa adaptabilidade deve-se à possibilidade de controle de sua composição química, microestrutura e tratamento térmico (CALLISTER; RETHWISCH, 2018). O controle dessas variáveis confere ao aço uma ampla gama de propriedades mecânicas, térmicas e químicas, adaptando-o a funções específicas.
2. Composição e Elementos de Liga
O aço é essencialmente composto por ferro (Fe) e carbono (C), com teor de carbono variando geralmente entre 0,02% e 2,11%. Além disso, outros elementos podem ser intencionalmente adicionados para conferir características específicas:
- Cromo (Cr): resistência à corrosão (aços inoxidáveis).
- Níquel (Ni): tenacidade e resistência ao impacto.
- Molibdênio (Mo): aumento da resistência à fluência a altas temperaturas.
- Vanádio (V): aumento da dureza e resistência ao desgaste.
Esses elementos influenciam diretamente a formação de microconstituintes como perlita, martensita e bainita (ASM HANDBOOK, 1990).
3. Classificação dos Aços
3.1 Aços Carbono
São os aços mais comuns, sem adição intencional de elementos de liga além do carbono.
- Baixo carbono (< 0,25%): dúcteis, usados em chapas e estruturas leves.
- Médio carbono (0,25–0,60%): melhor resistência mecânica, utilizados em engrenagens e eixos.
- Alto carbono (> 0,60%): elevada dureza, usados em molas e ferramentas de corte.
3.2 Aços Inoxidáveis
Contêm no mínimo 10,5% de cromo, formando uma camada passiva de óxido que impede a corrosão.
- Ferríticos: magnéticos, com baixo carbono.
- Austeníticos: não magnéticos, excelente resistência química (ex: AISI 304, 316).
- Martensíticos: podem ser temperados e revenidos.
3.3 Aços para Ferramentas
Projetados para resistência ao desgaste e manutenção de dureza a altas temperaturas. Podem ser classificados como:
- Aços rápidos (high-speed steels).
- Aços para moldes de injeção.
3.4 Aços Estruturais
Utilizados em pontes, edifícios, navios e plataformas, geralmente classificados pela resistência à tração (ex: ASTM A36, A992).
4. Normas Técnicas e Classificações
4.1 Sistema SAE/AISI
O sistema SAE (Society of Automotive Engineers) e AISI (American Iron and Steel Institute) classifica os aços segundo sua composição:
Série | Tipo | Exemplos |
---|---|---|
10XX | Aços carbono simples | 1020, 1045 |
41XX | Aços com Cr-Mo | 4140, 4130 |
43XX | Ni-Cr-Mo | 4340 |
50XX | Cr médio | 5150 |
86XX | Ni-Cr-Mo | 8620 |
Exemplo: SAE 1045 → aço carbono médio com 0,45% de C.
4.2 Normas Internacionais
- ASTM (American Society for Testing and Materials).
- DIN (Deutsches Institut für Normung).
- EN (European Norm).
- NBR (ABNT – Brasil).
A padronização garante intercambialidade, rastreabilidade e desempenho adequado conforme a aplicação (DIN, 2012).
5. Tratamentos Térmicos e Endurecimento
Tratamentos térmicos visam modificar a estrutura do aço, otimizando suas propriedades mecânicas.
5.1 Principais processos
- Têmpera: aquecimento seguido de resfriamento rápido → martensita.
- Revenimento: redução da fragilidade pós-têmpera.
- Normalização: estrutura fina e homogênea.
- Recozimento: aumenta ductilidade, alivia tensões internas.
5.2 Endurecimento Superficial
- Cementação: introdução de carbono na superfície.
- Nitretação: formação de camada de nitretos.
- Indução: aquecimento localizado com resfriamento controlado.
6. Aço Verde e Sustentabilidade
O conceito de aço verde envolve a redução das emissões de CO₂ e o uso de fontes renováveis nos processos siderúrgicos. Métodos emergentes incluem:
- Uso de H₂ (hidrogênio verde) como redutor no lugar de coque.
- Captura e armazenamento de carbono (CCS).
- Reaproveitamento de escória como material de construção.
Empresas como a SSAB (Suécia) e ArcelorMittal já implementam iniciativas de aço verde com baixo impacto ambiental (WORLD STEEL ASSOCIATION, 2022).
7. Pós-Produção: Reutilização e Reciclagem
O aço é 100% reciclável, mantendo suas propriedades. A sucata metálica é reincorporada na produção via forno elétrico ou como adição no conversor.
Vantagens:
- Redução de consumo energético (~70% menor que produção primária).
- Diminuição de resíduos sólidos.
- Redução da pegada de carbono.
8. Considerações
A compreensão das propriedades, classificações e tratamentos do aço é essencial para seu uso estratégico em diferentes setores industriais. Além da diversidade técnica, o avanço em direções sustentáveis, como o aço verde, destaca a importância da siderurgia em um contexto de responsabilidade ambiental. A normatização e a reciclagem complementam esse cenário, conferindo à cadeia do aço um papel-chave na economia circular global.
Referências
- ASM HANDBOOK. Volume 1: Properties and Selection – Irons, Steels, and High-Performance Alloys. ASM International, 1990.
- CALLISTER, W. D.; RETHWISCH, D. G. Materials Science and Engineering: An Introduction. 9. ed. New York: Wiley, 2018.
- DIN. Deutsches Institut für Normung – Werkstoffnormung: Stahl. Berlin: DIN Standards Committee, 2012.
- WORLD STEEL ASSOCIATION. Sustainable Steel – Indicators 2022 and Trends. Brussels: worldsteel, 2022.
Aplicações Industriais: O Coração da Infraestrutura Moderna
O aço é um dos pilares fundamentais da infraestrutura industrial contemporânea. Sua versatilidade, resistência mecânica e capacidade de ser moldado e reciclado o tornam um material insubstituível em diversos setores, da construção civil à indústria aeroespacial. Este artigo apresenta uma análise detalhada das aplicações industriais do aço, discutindo composições típicas, exigências técnicas, evolução histórica e tendências futuras.
Palavras-chave: aço, aplicações industriais, infraestrutura, construção, transporte, inovação tecnológica.
1. Introdução
Desde a Revolução Industrial, o aço tem desempenhado papel central no desenvolvimento das economias modernas. Sua presença é marcante em praticamente todos os segmentos produtivos, sendo considerado um indicador do grau de industrialização de um país (WORLD STEEL ASSOCIATION, 2022). A maleabilidade e resistência do aço permitem aplicações diversas, que vão desde grandes obras de engenharia até peças de alta precisão.
2. Construção Civil: Estrutura e Sustentação
2.1 Estruturas Metálicas e Concreto Armado
Na construção civil, o aço é amplamente empregado em:
- Pontes metálicas (ex: Ponte Rio-Niterói, Brasil): utilização de perfis estruturais de aço ASTM A36 ou A992.
- Arranha-céus: sistemas mistos com aço estrutural (pilares, vigas) e concreto (lajes).
- Galpões industriais: estruturas modulares com chapas e perfis dobrados a frio.
O uso do aço permite maior rapidez na execução, redução de cargas nas fundações e facilidade de desmontagem e reaproveitamento.
2.2 Aço CA-50/CA-60
Empregado no concreto armado, esses vergalhões possuem resistência à tração de 500 a 600 MPa, com composição típica contendo carbono (~0,25%), manganês e pequenas quantidades de silício.
3. Setor Automotivo: Leveza e Resistência em Movimento
A indústria automobilística tem avançado no uso de aços de alta resistência (AHSS) e aços ultrarresistentes (UHSS), com o objetivo de reduzir peso e emissões, mantendo segurança.
3.1 Componentes Automotivos
- Estrutura da carroceria: aços dual phase (DP600, DP800) combinam ductilidade e resistência.
- Motores e sistemas de transmissão: aços liga 4340, com Cr-Ni-Mo, pela elevada tenacidade.
- Suspensões e molas: aço mola SAE 5160.
3.2 Evolução
De veículos robustos com chapas espessas (décadas de 1950–1970) para carros leves, modulares e seguros, como os produzidos pelas plataformas da Volkswagen MQB ou da Toyota TNGA.
4. Indústria Naval e Offshore
A construção naval exige aços com resistência à corrosão marinha, tenacidade e soldabilidade.
- Aço naval ASTM A131: usado em cascos de navios, possui adições de manganês e silício.
- Plataformas de petróleo: estruturas em aço ASTM A572, projetadas para ambientes agressivos.
- Submarinos e cascos pressurizados: uso de aços com elevado limite de escoamento e controle de ferriticidade.
O aço permite manutenção simplificada, alta resistência à fadiga e longa vida útil.
5. Indústria Aeroespacial: Precisão e Alta Performance
Apesar do uso crescente de ligas leves (alumínio, titânio e materiais compostos), o aço ainda é fundamental em partes críticas de aeronaves:
- Trem de pouso: aço 300M (Cr-Ni-Mo), com resistência superior a 1.900 MPa.
- Eixos e flanges: aços inoxidáveis e martensíticos.
- Turbinas de avião (partes internas): aço inox refratário, capaz de operar a altas temperaturas.
Com a miniaturização e automação, o setor aeroespacial requer altíssima precisão dimensional e integridade estrutural.
6. Máquinas, Ferramentas e Eletrodomésticos
6.1 Aços para ferramentas
Ferramentas de corte, moldes de injeção e matrizes usam aços como:
- AISI H13: resistência térmica e ao choque.
- AISI D2: elevada dureza e resistência ao desgaste.
6.2 Eletrodomésticos
Chapas finas de aço galvanizado ou inoxidável são amplamente usadas em:
- Refrigeradores (inoxidáveis 430).
- Máquinas de lavar e fornos.
- Estruturas internas de micro-ondas e ar-condicionado.
O aço inox garante durabilidade, estética e resistência à oxidação.
7. Tendências Futuras: Inovação e Sustentabilidade
7.1 Impressão 3D e Manufatura Aditiva
Aços inoxidáveis e aços maraging estão sendo usados em fabricação aditiva de peças estruturais complexas para aeronaves, motores e ferramentas sob demanda.
7.2 Aços Inteligentes e Sustentáveis
- Aço verde: produzido com hidrogênio, redução direta e baixa emissão de CO₂.
- Smart steels: sensores embutidos em estruturas para monitoramento ativo.
7.3 Circularidade e Indústria 4.0
Com sensores e controle digital, máquinas inteligentes podem detectar falhas, planejar manutenção e otimizar o uso do aço em tempo real, reduzindo desperdícios.
8. Considerações
O aço se consolidou como um material essencial à infraestrutura moderna, permeando indústrias críticas como construção, transporte, energia e tecnologia. Sua evolução acompanha os avanços tecnológicos e as necessidades da sociedade por materiais mais leves, eficientes e sustentáveis. O futuro do aço está na inovação aliada à circularidade e descarbonização, reafirmando seu papel como espinha dorsal da indústria global.
Referências
- CALLISTER, W. D.; RETHWISCH, D. G. Fundamentals of Materials Science and Engineering. 9. ed. New York: Wiley, 2018.
- ASM INTERNATIONAL. Metals Handbook Desk Edition. 2nd ed. Materials Park, Ohio: ASM, 1998.
- WORLD STEEL ASSOCIATION. Steel Statistical Yearbook 2022. Brussels: Worldsteel, 2022.
- SAE INTERNATIONAL. SAE J403 – Chemical Compositions of SAE Carbon Steels. Warrendale, PA, 2020.
- DIN. Werkstoffnormung – Stahl und Stahlprodukte. Berlin: Deutsches Institut für Normung, 2012.
Sustentabilidade e Futuro da Siderurgia
Diante dos crescentes desafios ambientais e da pressão global por descarbonização, o setor siderúrgico encontra-se em um momento de transição tecnológica e estratégica. Este artigo explora as principais inovações sustentáveis no setor, como o uso do hidrogênio como agente redutor, reciclagem de sucata metálica, biometano, economia circular e a aplicação dos princípios da Indústria 4.0 para otimização de processos, com foco em eficiência energética, redução de emissões e responsabilidade socioambiental.
Palavras-chave: siderurgia verde, hidrogênio, economia circular, biometano, Indústria 4.0, sustentabilidade.
1. Introdução
A siderurgia é uma das indústrias mais intensivas em energia e emissora de gases de efeito estufa (GEE), sendo responsável por cerca de 7% das emissões globais de CO₂ (IEA, 2021). Nesse cenário, a busca por soluções tecnológicas sustentáveis tornou-se prioridade para garantir a continuidade da produção de aço diante das metas climáticas globais, como as previstas no Acordo de Paris.
2. Economia Circular e Reciclagem do Aço
2.1 O Ciclo Infinito do Aço
O aço é 100% reciclável sem perda de propriedades mecânicas, o que o torna um dos pilares da economia circular na indústria de base. Segundo a World Steel Association (2022), mais de 630 milhões de toneladas de aço foram recicladas globalmente em 2021.
2.2 Forno de Arco Elétrico (EAF)
A reciclagem de sucata metálica via forno de arco elétrico (EAF) permite uma produção com até 70% menos emissões de CO₂ do que os altos-fornos convencionais. É o método predominante em países como os EUA e ganha espaço no Brasil, impulsionado por:
- Crescimento da oferta de sucata urbana e industrial.
- Menor dependência de minério de ferro e carvão.
- Possibilidade de integração com fontes de energia renováveis.
3. Energias Alternativas: Biometano e Hidrogênio Verde
3.1 Biometano a partir de Aterros Sanitários
O biometano, produzido a partir da digestão anaeróbica de resíduos sólidos urbanos (RSU), surge como alternativa limpa ao gás natural na siderurgia. Iniciativas-piloto já operam em siderúrgicas brasileiras como a ArcelorMittal, usando biometano para substituir parcialmente combustíveis fósseis nos fornos de reaquecimento.
3.2 Hidrogênio Verde como Redutor
O uso do hidrogênio (H₂) como redutor no processo de obtenção de ferro (DRI – Direct Reduced Iron) representa a fronteira mais avançada da siderurgia verde. Essa substituição do coque por H₂ no processo de redução direta permite:
- Redução de até 95% nas emissões de CO₂.
- Produção de água como subproduto, ao invés de dióxido de carbono.
- Integração com fontes renováveis (eólica, solar).
Exemplo notável é o projeto HYBRIT (Suécia), parceria entre a SSAB, LKAB e Vattenfall, pioneiro na produção de aço livre de fósseis.
4. Indústria 4.0 e Siderurgia Digital
A digitalização é essencial para aumentar a eficiência energética, prever falhas e reduzir desperdícios nos processos siderúrgicos. As tecnologias incluem:
- Sensores IoT em equipamentos para monitoramento em tempo real.
- Gêmeos digitais para simular e otimizar processos como a aciaria e a laminação.
- Big data e inteligência artificial (IA) aplicados na manutenção preditiva e controle de qualidade.
- Automação robótica em áreas de alto risco ou precisão, como manuseio de lingotes ou amostragem de aço líquido.
A Gerdau, por exemplo, já utiliza IA e machine learning para otimizar rotas metalúrgicas e prever consumo de energia em suas plantas.
5. Eficiência Energética e Novos Processos
5.1 Sinterização com Menor Emissão
O uso de técnicas como injeção de biomassa e aglomerantes alternativos na sinterização do minério de ferro reduz o consumo de coque e as emissões de gases tóxicos como NOx e SOx.
5.2 Captura e Armazenamento de Carbono (CCS)
Algumas siderúrgicas estão investindo em tecnologias de captura e armazenamento de CO₂, principalmente em plantas integradas, para atender às legislações ambientais e obter créditos de carbono.
6. Desafios e Oportunidades
Apesar dos avanços, a transição para uma siderurgia sustentável enfrenta obstáculos:
- Alto custo inicial das tecnologias verdes (especialmente hidrogênio verde).
- Necessidade de infraestrutura para geração e transporte de energias renováveis.
- Competitividade global e desigualdade regulatória entre países.
Entretanto, surgem oportunidades associadas à reputação sustentável, acesso a novos mercados e incentivos financeiros por meio de políticas climáticas, fundos verdes e exigências da União Europeia (CBAM – Carbon Border Adjustment Mechanism).
7. Considerações
A siderurgia do futuro será limpa, digital, circular e conectada às energias renováveis. A adoção de práticas sustentáveis não é apenas uma resposta ética e ambiental, mas um imperativo estratégico e econômico. O aço verde, produzido com eficiência e responsabilidade, será a base de uma nova era industrial orientada para a sustentabilidade e a inovação.
Referências
- IEA – International Energy Agency. Iron and Steel Technology Roadmap. Paris: OECD, 2021.
- WORLD STEEL ASSOCIATION. Sustainable Steel – Indicators 2022 and Progress Report. Brussels: Worldsteel, 2022.
- HYBRIT Development. Fossil-free steel. Available at: https://www.hybritdevelopment.se/
- GERDAU. Relatório de Sustentabilidade 2022. São Paulo: Gerdau, 2022.
- SILVA, R. M.; AMORIM, D. C. O uso de biometano na siderurgia brasileira: potencialidades e desafios. Revista de Energia e Sustentabilidade, v. 10, n. 2, 2023.
- CALLISTER, W. D. Materials Science and Engineering: An Introduction. 9. ed. Wiley, 2018.
Conclusão
Da solidez dos minerais ao brilho das estruturas metálicas, a trajetória do aço simboliza o engenho humano em transformar os recursos naturais em motores do progresso. Com um olhar atento à sustentabilidade, a indústria pode continuar forjando o futuro com responsabilidade.
Classificação
A classificação das indústrias siderúrgicas com base na capacidade de produção de aço é fundamental para compreender a estrutura e a dinâmica do setor. Embora não exista uma padronização universalmente aceita, é comum segmentar as usinas siderúrgicas em categorias como grande porte, médio porte e pequeno porte, tomando como referência a produção anual de aço bruto.
Classificações Comuns por Capacidade de Produção
- Grande Porte: Usinas com produção anual superior a 10 milhões de toneladas de aço bruto.
- Médio Porte: Usinas que produzem entre 1 milhão e 10 milhões de toneladas anualmente.
- Pequeno Porte: Usinas com produção inferior a 1 milhão de toneladas por ano.
Essas categorias são utilizadas para análises de mercado, benchmarking e formulação de políticas industriais.
Exemplos de Produtores de Aço por Porte
Grandes Produtores:
- China Baowu Steel Group: Maior produtor mundial, com 130,77 milhões de toneladas em 2023.
- ArcelorMittal: Produção de 68,52 milhões de toneladas em 2023.
- Ansteel Group: Produção de 55,89 milhões de toneladas em 2023.
Fonte: List of steel producers
Produtores de Médio Porte:
- Ternium: Com capacidade de produção de 15,4 milhões de toneladas anuais.
- Gerdau: Produziu 12,74 milhões de toneladas em 2023.
Fontes: Ternium, List of steel producers
Produtores de Pequeno Porte:
- Libyan Iron and Steel Company (LISCO): Capacidade de aproximadamente 1,324 milhão de toneladas de aço líquido por ano.
Fonte: Libyan Iron and Steel Company
Considerações sobre a Classificação
É importante destacar que essas classificações não são rígidas e podem variar conforme a fonte e o contexto. Além disso, fatores como integração vertical, diversidade de produtos e presença geográfica também influenciam a relevância e o impacto de uma empresa no mercado siderúrgico.
Por exemplo, o Grupo Techint, embora não listado entre os maiores produtores de aço bruto, possui significativa influência no setor por meio de suas subsidiárias Tenaris e Ternium, que operam em diversos países e segmentos da indústria siderúrgica. A Tenaris é líder na produção de tubos de aço para a indústria petrolífera, enquanto a Ternium destaca-se na produção de aços planos para construção e indústria automotiva.
Fonte: Techint
Portanto, ao avaliar o porte e a importância de uma siderúrgica, é essencial considerar não apenas a capacidade de produção, mas também a diversificação de produtos, mercados atendidos e estratégias corporativas.

Classificação das Indústrias Siderúrgicas por Porte: Uma Análise Baseada na Capacidade de Produção de Aço
A capacidade de produção anual de aço é um dos principais critérios utilizados para classificar indústrias siderúrgicas quanto ao seu porte. Essa categorização permite compreender a escala de operação, a influência mercadológica e a abrangência territorial das empresas do setor. O presente artigo discute as classificações comuns de porte das siderúrgicas — pequeno, médio, grande e mega —, com base em dados atualizados e exemplos de players relevantes no cenário mundial.
1. Introdução
A indústria siderúrgica é um dos pilares da infraestrutura e do desenvolvimento econômico mundial. A classificação das usinas siderúrgicas conforme sua capacidade de produção anual de aço é um critério amplamente utilizado para avaliar o impacto econômico e tecnológico dessas empresas. Além disso, essa categorização oferece parâmetros úteis para análises comparativas entre empresas, investimentos e políticas industriais.
2. Classificações Comuns por Capacidade de Produção
A seguir, apresenta-se uma proposta de categorização com base em faixas de produção anual de aço bruto (em milhões de toneladas):
Categoria | Capacidade de Produção (t/ano) |
---|---|
Mega-siderúrgicas | Acima de 10 milhões |
Grande porte | 5 a 10 milhões |
Médio porte | 2 a 5 milhões |
Pequeno porte | Abaixo de 2 milhões |
2.1 Mega-siderúrgicas
Empresas com capacidade produtiva superior a 10 milhões de toneladas anuais. Possuem forte presença internacional, operações verticalizadas e impacto direto nas políticas globais de precificação e oferta de aço.
Exemplos:
- China Baowu Steel Group: >130 milhões t/ano.
- ArcelorMittal: ~68 milhões t/ano.
- Nippon Steel: ~50 milhões t/ano.
2.2 Siderúrgicas de Grande Porte
Empresas com capacidade entre 5 e 10 milhões de toneladas por ano. Costumam operar regionalmente com alguma internacionalização, tendo relevância estratégica para o desenvolvimento industrial local.
Exemplos:
- Gerdau: ~12,7 milhões t/ano.
- Ternium (Techint Group): ~14,8 milhões t/ano (classificada na 26ª posição mundial, segundo worldsteel).
2.3 Siderúrgicas de Médio Porte
Com produção entre 2 e 5 milhões de toneladas por ano, essas empresas geralmente são especializadas ou operam fortemente em setores específicos, como construção, energia ou automobilismo.
Exemplos:
- Hyundai Steel, dependendo da planta.
- Diversas empresas indianas e russas com atuação regional.
2.4 Siderúrgicas de Pequeno Porte
Produção inferior a 2 milhões de toneladas anuais. Em geral, atendem nichos de mercado ou operam localmente com foco em produtos especializados como aços inoxidáveis, especiais ou ferramentas.
Exemplos:
- Pequenas siderúrgicas regionais ou familiares.
- Empresas dedicadas a aços especiais ou inoxidáveis.
3. Impactos da Capacidade de Produção
Empresas de grande e mega porte influenciam diretamente o mercado global, sendo responsáveis por definir tendências de preço, avanços tecnológicos e normativos. Já as siderúrgicas menores têm papel fundamental na inovação aplicada a nichos e na resposta rápida às necessidades de mercados regionais ou específicos.
4. Considerações
A classificação por capacidade de produção revela mais do que apenas o volume produtivo: indica também o grau de integração vertical, o alcance de mercado e a sofisticação tecnológica das siderúrgicas. A compreensão dessas categorias é fundamental para análises setoriais, investimentos estratégicos e formulação de políticas públicas de fomento industrial.
Referências Bibliográficas
- World Steel Association. Top Steel-Producing Companies 2023. Disponível em: https://worldsteel.org/data/top-producers
- Wikipedia. List of Steel Producers. Disponível em: https://en.wikipedia.org/wiki/List_of_steel_producers
- Wikipedia. Techint. Disponível em: https://en.wikipedia.org/wiki/Techint
- TERNIUM. Annual Reports and Production Capacity. Disponível em: https://www.ternium.com
- Gerdau. Relatório Anual e Sustentabilidade. Disponível em: https://www.gerdau.com
Techint Group: Um Gigante Global em Siderurgia, Engenharia e Sustentabilidade
O Techint Group é um conglomerado industrial multinacional fundado em 1945, com sede em Milão (Itália) e atuação global, especialmente destacada na América Latina. Por meio de suas subsidiárias — como a Ternium (siderurgia), Tenaris (tubos e serviços para a indústria de petróleo e gás), e a Techint Engenharia e Construção — o grupo desenvolve projetos de larga escala nos setores de siderurgia, energia, petróleo e gás, infraestrutura e sustentabilidade.
Siderurgia: Ternium e o Papel do Techint na Produção Global de Aço
A Ternium, subsidiária siderúrgica do grupo, é uma das maiores produtoras de aço da América Latina, com presença em países como Brasil, Argentina, México e Colômbia. O Techint Group ocupa a 26ª posição no ranking global de maiores produtores de aço, com uma capacidade anual significativa (World Steel Association, 2023).
A Ternium opera com tecnologias modernas, incluindo fornos de arco elétrico (que utilizam sucata metálica reciclada) e processos de dessulfuração e conformação que agregam valor à cadeia produtiva do aço (Ternium, 2024).
Engenharia e Construção: Grandes Projetos de Infraestrutura e Energia
A divisão de Engenharia e Construção do grupo é responsável por uma série de obras icônicas na América Latina e em outros continentes. Destacam-se:
- Oleoduto de Vaca Muerta (Argentina): projeto de infraestrutura para transporte de petróleo e gás não convencionais.
- Campo de Libra (Brasil): participação em obras de exploração offshore no pré-sal brasileiro.
- Hidrelétrica de Belo Monte (Brasil): contribuição para a construção de uma das maiores usinas hidrelétricas do mundo.
- Metropolitano de São Paulo (Brasil) e obras urbanas em Caracas (Venezuela): infraestrutura de transporte e urbanização (Techint Engenharia e Construção, 2024).
Sustentabilidade: Compromisso com a Transição Energética
O grupo adota políticas ambientais alinhadas aos Objetivos de Desenvolvimento Sustentável (ODS). Entre as iniciativas destacam-se:
- Uso de biometano (Brasil): em Seropédica (RJ), a Ternium utiliza biometano gerado a partir de aterros sanitários, substituindo gás natural e reduzindo emissões de CO₂.
- Parques eólicos e solares (Argentina e México): investimento crescente em geração de energia limpa (Techint, 2024).
- Reciclagem industrial: uso intensivo de sucata metálica em fornos de arco elétrico e reaproveitamento de resíduos industriais nos processos produtivos.
- Certificação ISO 14001: sistemas de gestão ambiental implementados em diversas subsidiárias.
Essas ações evidenciam um alinhamento com o conceito de economia circular, promovendo eficiência energética e redução de impactos ambientais.
Projetos de Energia Renovável:
O Techint tem investido em energia limpa e renovável como parte de sua estratégia para reduzir a pegada de carbono e apoiar a transição energética.
Parques Eólicos e Solares (Argentina e México): O Techint tem participação no desenvolvimento de parques eólicos e centrais solares na Argentina e México. Esses projetos visam gerar energia limpa e renovável, reduzindo a dependência de fontes fósseis e contribuindo para as metas de descarbonização.
Exemplo: Parque Eólico Vientos de Montalto (Argentina): O Techint participou da construção e operação de um grande parque eólico em Montalto, na província de Buenos Aires, com o objetivo de gerar energia eólica para o sistema elétrico nacional da Argentina.
Geração de Energia Solar no México: O Techint também está envolvido em projetos solares no México, com iniciativas voltadas para a construção de fazendas solares em várias regiões do país, aumentando a capacidade de geração de energia limpa e ajudando a diversificar a matriz energética.
Siderurgia Sustentável (Ternium):
A Ternium, uma das principais subsidiárias do Techint, está focada em reduzir o impacto ambiental de suas operações, especialmente no setor siderúrgico, um dos mais intensivos em carbono.
Projeto de Produção de Biometano (Brasil): A Ternium no Brasil iniciou um projeto de biometano em Seropédica (RJ), transformando o metano proveniente de aterros sanitários em biometano, um combustível renovável. Este biometano é utilizado nas operações industriais, substituindo o uso de gás natural e reduzindo as emissões de CO₂.
Uso de Energia Renovável: A Ternium tem investido em fontes de energia renováveis, como energia solar e energia eólica, para complementar suas operações, melhorando a eficiência energética e diminuindo o impacto ambiental de suas atividades.
Reciclagem de Sucata: A reciclagem de sucata metálica é uma das principais estratégias da Ternium para reduzir o uso de matérias-primas e reduzir suas emissões. A empresa recicla metal reciclado em larga escala para a produção de aço, o que diminui a necessidade de minério de ferro e outros recursos não renováveis.
Infraestrutura Sustentável:
No setor de engenharia e construção, o Techint está implementando projetos de infraestrutura verde e buscando otimizar a eficiência energética e redução de impactos ambientais nas obras de construção.
Projetos de Infraestrutura Ecológica: O Techint tem desenvolvido infraestruturas sustentáveis para setores como saneamento, gestão de resíduos e tratamento de águas residuais. Esses projetos são projetados para minimizar os impactos ambientais, melhorar a eficiência no uso de recursos naturais e promover a reciclagem de resíduos.
Edificações Sustentáveis: O grupo tem se envolvido em projetos de construção de edifícios sustentáveis, aplicando práticas de eficiência energética, como o uso de materiais reciclados, sistemas de coleta de águas pluviais, e tecnologias para reduzir o consumo de energia nas construções.
Gestão de Resíduos e Economia Circular:
O Techint também está comprometido com a gestão de resíduos e a promoção da economia circular em seus processos industriais.
Reciclagem de Resíduos Industriais: A Ternium, por exemplo, tem trabalhado na reciclagem de resíduos provenientes da produção de aço, utilizando esses materiais em novos processos produtivos. Isso ajuda a reduzir o desperdício e a preservar recursos naturais, além de diminuir o impacto ambiental.
Projetos de Gestão de Resíduos Urbanos: O Techint tem participado de projetos que visam melhorar a gestão de resíduos urbanos, como planta de compostagem e reciclagem de resíduos sólidos em diversas cidades onde tem operações. O objetivo é reduzir a quantidade de lixo enviado para aterros e promover a reutilização de materiais.
Compromissos com a Sustentabilidade e Certificações Ambientais:
O Techint Group adota práticas empresariais responsáveis, alinhando suas operações com padrões globais de sustentabilidade e responsabilidade ambiental.
Certificação ISO 14001: Diversas subsidiárias do Techint, incluindo a Ternium, têm implementado sistemas de gestão ambiental (SGA) com base na ISO 14001, garantindo a redução de impactos ambientais e a melhoria contínua das práticas de sustentabilidade.
Relatórios de Sustentabilidade: O Techint também publica anualmente relatórios de sustentabilidade, nos quais compartilha dados sobre suas iniciativas ambientais, como redução de emissões, uso eficiente de recursos e desenvolvimento de soluções sustentáveis.
O Techint Group está comprometido com a sustentabilidade em várias frentes, desde a energia renovável até a reciclagem industrial e a gestão de resíduos, com foco na redução das emissões de carbono e na implementação de soluções que favoreçam a economia circular. Sua atuação nas indústrias de energia, siderurgia e engenharia e construção está alinhada com as tendências globais de sustentabilidade e transição energética, garantindo que seus projetos e operações minimizem impactos ambientais e contribuam para um futuro mais sustentável.
Conclusão
O Techint Group se posiciona como um dos principais conglomerados industriais do mundo, não apenas por sua produção siderúrgica, mas por sua atuação estratégica em projetos de engenharia, energia e infraestrutura. Ao mesmo tempo, destaca-se como referência em práticas sustentáveis, contribuindo para a descarbonização da indústria pesada.
Referências
- TECHINT Group. Techint Engenharia e Construção. Disponível em: https://www.techintgroup.com. Acesso em: 09 abr. 2025.
- Ternium. Relatório de Sustentabilidade 2023. Disponível em: https://www.ternium.com. Acesso em: 09 abr. 2025.
- World Steel Association. List of Steel Producers. Wikipedia, 2023. Disponível em: https://en.wikipedia.org/wiki/List_of_steel_producers. Acesso em: 09 abr. 2025.
- Wikipedia. Techint. Wikipedia, 2023. Disponível em: https://en.wikipedia.org/wiki/Techint. Acesso em: 09 abr. 2025.
- ISO. ISO 14001 Environmental management systems. Disponível em: https://www.iso.org/iso-14001-environmental-management.html. Acesso em: 09 abr. 2025.
Techint Group ocupa a 26ª posição no ranking global de maiores produtores de aço. O Techint é um conglomerado multinacional que opera em diversas áreas industriais, incluindo engenharia, construção, energia e, especialmente, siderurgia através de sua unidade Ternium.
O grupo é uma das grandes potências no setor de siderurgia e engenharia, com presença significativa na América Latina e em outros mercados globais. A Ternium, sua subsidiária siderúrgica, é responsável por uma grande parte da produção de aço na América Latina, mas o Techint como um todo, incluindo outras áreas de atuação, alcança a 26ª posição em termos de capacidade de produção de aço no ranking global.
Algumas informações adicionais sobre o Techint Group:
Ternium: Sua principal subsidiária siderúrgica, que é um dos maiores produtores de aço da América Latina. A Ternium tem uma capacidade significativa de produção, com plantas em países como Brasil, Argentina, México e Colômbia.
Outras áreas de atuação: O Techint também tem grande presença no setor de engenharia e construção, realizando grandes projetos de infraestrutura e petróleo e gás, além de atuar em energia e indústrias químicas.
O ranking global de produtores de aço é dominado por gigantes como China Baowu Steel Group, ArcelorMittal e HBIS Group, mas o Techint, com sua operação diversificada, se destaca entre as grandes corporações do setor.
O Techint Group é um conglomerado global que atua em diversos setores, e sua presença no setor de engenharia e construção é notável, com uma série de grandes projetos de infraestrutura, petróleo e gás, energia e indústrias químicas ao redor do mundo. A empresa é conhecida por sua capacidade de executar grandes projetos de engenharia de grande escala, muitas vezes em condições desafiadoras.
Aqui estão alguns exemplos de projetos relevantes e locais onde o Techint Group tem atuado:
- Setor de Petróleo e Gás:
O Techint tem uma forte presença no setor de petróleo e gás, fornecendo serviços de engenharia, procurement, construção e manutenção (EPCM), além de participar na construção de oleodutos, gasodutos e instalações de processamento de petróleo e gás.
Oleoduto de Vaca Muerta (Argentina): O Techint foi um dos principais responsáveis pela construção de um dos maiores oleodutos do mundo, no campo de Vaca Muerta, na Argentina, que é um dos maiores depósitos de petróleo e gás não convencionais (xisto) do planeta. Este projeto envolveu a construção de infraestrutura significativa para o transporte de petróleo e gás.
Projeto no Campo de Libra (Brasil): O grupo tem atuado no desenvolvimento e construção de infraestruturas de exploração e produção de petróleo em campos offshore no Brasil, incluindo projetos em campos como o Libra, um dos maiores do pré-sal.
- Setor de Energia:
O Techint também é um player significativo no setor de energia, com atuação em projetos de geração de energia, transmissão e distribuição de eletricidade, além de soluções de energia renovável.
Central Hidrelétrica Belo Monte (Brasil): O Techint participou da construção da Central Hidrelétrica Belo Monte, uma das maiores hidrelétricas do mundo, localizada no Rio Xingu, no estado do Pará, no Brasil. A construção envolveu um grande esforço de engenharia para a infraestrutura elétrica e as instalações de geração de energia.
Energia Renovável (Argentina): O Techint também tem se envolvido em projetos de energia renovável, incluindo a instalação de parques solares e eólicos na Argentina e em outros países da América Latina, como parte de sua estratégia para expandir sua participação em fontes de energia limpa e sustentável.
- Infraestrutura e Construção Civil:
Além do setor energético, o Techint tem uma longa história no setor de construção de infraestrutura. A empresa participa de grandes projetos de infraestrutura urbana e industrial, como pontes, estradas, ferrovias, aeroportos e portos.
Construção do Metropolitano de São Paulo (Brasil): O Techint participou da construção de partes do metrô de São Paulo, incluindo a construção de estações e túneis do sistema metroviário da cidade.
Ponte de Panamá (Panamá): O grupo foi responsável pela construção de pontes e viadutos em várias partes do Panamá, incluindo a construção de infraestrutura crítica no país.
Projeto de Infraestrutura em Caracas (Venezuela): O Techint esteve envolvido na construção e modernização de infraestruturas urbanas e industriais na capital da Venezuela, Caracas, incluindo grandes projetos de habitação e desenvolvimento urbano.
- Indústria Química:
O Techint também participa de projetos no setor químico e petroquímico, construindo plataformas industriais e unidades de refinamento de petróleo, produção de produtos químicos e fertilizantes.
Plantas Petroquímicas no México: O Techint tem participação em grandes projetos petroquímicos no México, incluindo a construção de unidades de refino de petróleo e plantas de produções de plásticos e fertilizantes.
- Setor de Saneamento e Tratamento de Água:
O Techint também tem participado em projetos de saneamento e tratamento de água em várias partes do mundo, ajudando a construir estacionamentos de tratamento de esgoto, plantas de dessalinização e sistemas de distribuição de água potável.
Sistema de Abastecimento de Água em Buenos Aires (Argentina): O grupo tem contribuído para o desenvolvimento de sistemas de abastecimento de água e esgoto na cidade de Buenos Aires, que envolvem a construção de infraestrutura de tratamento de águas residuais e a expansão do fornecimento de água potável.
O Techint Group tem uma presença global significativa e está envolvido em projetos de grande porte em diversos setores, incluindo petróleo e gás, energia, infraestrutura de transporte e construção civil, e indústria química. A empresa tem contribuído para a construção de grandes projetos industriais, de infraestrutura e energéticos na América Latina, bem como em várias outras partes do mundo, com um forte portfólio de parcerias públicas e privadas.
O Parque Industrial da Ternium em Santa Cruz (RJ): Capacidade Produtiva, Sustentabilidade e Perspectivas Futuras
O setor siderúrgico brasileiro ocupa posição estratégica na economia nacional, não apenas pela produção de insumos essenciais para a construção civil, indústria automotiva e infraestrutura, mas também pela sua relação com a inovação tecnológica e sustentabilidade ambiental. Nesse contexto, destaca-se o parque industrial da Ternium Brasil, localizado em Santa Cruz, na zona oeste da cidade do Rio de Janeiro. Esta unidade representa uma das mais modernas e importantes plantas siderúrgicas da América Latina, com capacidade integrada de produção de aço e foco em práticas industriais alinhadas às metas globais de descarbonização.
Histórico e Implantação
A implantação do parque industrial teve início em 2008, com a construção da Companhia Siderúrgica do Atlântico (CSA), fruto de uma joint venture entre a Thyssenkrupp e a Vale. Inaugurada em 2010, a planta foi concebida como uma siderúrgica integrada, com acesso estratégico ao Porto de Sepetiba, facilitando a logística de importação de carvão mineral e exportação de aço. Em 2017, a Ternium adquiriu a planta da Thyssenkrupp, incorporando-a ao seu portfólio e promovendo a modernização da estrutura industrial existente (Ternium, 2023).
Capacidade Produtiva e Características Técnicas
A planta de Santa Cruz possui capacidade instalada de aproximadamente 5 milhões de toneladas de placas de aço por ano, operando com altos-fornos integrados e aciarias modernas. O complexo industrial inclui unidades de coqueria, sinterização, alto-forno, convertedor BOF, lingotamento contínuo e laminação. Além disso, a planta é dotada de uma infraestrutura logística robusta, com terminal ferroviário, acesso portuário e armazéns de grande porte (World Steel Association, 2022).
Produtos e Principais Mercados
A unidade produz placas de aço, bobinas laminadas a quente e a frio, além de chapas galvanizadas, destinadas a setores como construção civil, indústria automotiva, naval, eletrodomésticos e infraestrutura. Parte significativa da produção é destinada ao mercado interno brasileiro, mas há também uma expressiva atividade de exportação, sobretudo para países das Américas, Europa e Ásia.
Sustentabilidade e Economia Circular
Desde sua aquisição, a Ternium tem investido fortemente na adaptação ambiental do parque industrial. Entre as principais ações destaca-se o uso crescente de biometano como substituto do gás natural, reduzindo significativamente as emissões de CO₂. Além disso, a unidade implementou o reaproveitamento de subprodutos como escória e gases de processo para geração de energia interna.
A adoção de sucata metálica como matéria-prima secundária vem sendo ampliada, promovendo a economia circular e a redução da dependência do minério de ferro primário. Segundo a Ternium (2024), aproximadamente 25% do aço produzido atualmente já incorpora material reciclado.
Investimentos em Inovação e Futuro Sustentável
A companhia anunciou que, até 2030, serão investidos R$ 650 milhões em projetos ambientais e de inovação tecnológica na planta de Santa Cruz. Esses recursos incluem melhorias em controle de emissões atmosféricas, tratamento de efluentes, automação industrial e digitalização dos processos de produção. A perspectiva de médio e longo prazo envolve a adoção de tecnologias como fornos elétricos a arco alimentados por energia renovável e maior integração com fontes limpas de energia, como parques solares e eólicos (Ternium, 2024).
Considerações
O parque industrial da Ternium em Santa Cruz representa não apenas um polo de produção siderúrgica de grande escala, mas também um exemplo de transformação rumo à indústria 4.0 e à descarbonização industrial. Com uma combinação de alta capacidade técnica, compromisso ambiental e inserção estratégica no mercado global, a unidade consolida-se como uma referência em sustentabilidade e inovação no setor siderúrgico brasileiro.
Referências
- Ternium. (2023). Relatório de Sustentabilidade Ternium Brasil. Disponível em: https://br.ternium.com
- Ternium. (2024). Investimentos em Sustentabilidade e Tecnologia no Rio de Janeiro. Acesso em abril de 2025.
- World Steel Association. (2022). Steel Statistical Yearbook. Disponível em: https://worldsteel.org
- Agência Brasil. (2023). “Ternium investe em biometano e energia limpa no RJ”. Disponível em: https://agenciabrasil.ebc.com.br
Iniciativas de Sustentabilidade e o Compromisso com o “Aço Verde”
A busca por uma siderurgia de baixo carbono tem impulsionado empresas globais a reestruturarem suas práticas operacionais. A Ternium Brasil, alinhada a esse movimento, tem adotado um conjunto de estratégias ambientais no parque industrial de Santa Cruz (RJ) com o objetivo de produzir o chamado “aço verde” — conceito que abrange a produção de aço com baixa emissão de gases de efeito estufa (GEE), economia circular, e autossuficiência energética.
Uso de Sucata Metálica
Uma das principais frentes sustentáveis da empresa é o uso intensivo de sucata metálica reciclada como insumo no processo siderúrgico. A Ternium investiu cerca de R$ 100 milhões na modernização de seus sistemas logísticos e industriais para viabilizar o aumento do reaproveitamento de sucata. Com essa medida, espera-se ampliar em 80% o volume de material reciclado utilizado na aciaria, substituindo progressivamente o minério de ferro como matéria-prima principal.
Esse modelo reduz significativamente a emissão de CO₂ por tonelada de aço produzido, além de diminuir a demanda por recursos naturais, promovendo uma cadeia circular de valor (Estadão, 2023; UOL Economia, 2023).
Utilização de Biometano
A Ternium também se tornou pioneira no uso de biometano na produção de aço no Brasil, desde 2019. O gás renovável, obtido por meio da decomposição de resíduos orgânicos no aterro sanitário de Seropédica (RJ) e fornecido pela empresa Gás Verde, substitui parte do gás natural fóssil tradicionalmente empregado no aquecimento dos altos-fornos e caldeiras industriais.
Essa iniciativa reduz significativamente a pegada de carbono do processo siderúrgico e representa um marco no setor industrial brasileiro, ao integrar fontes renováveis à matriz energética de uma indústria intensiva em energia (Brazil Journal, 2023; Notícias de Mineração Brasil, 2023).
Projetos Ambientais e Governança ESG
Além das mudanças operacionais, a Ternium anunciou investimentos da ordem de R$ 650 milhões até 2030 em projetos ambientais no parque de Santa Cruz. Os aportes contemplam modernizações em sistemas de filtragem de partículas, controle de emissões atmosféricas, tratamento de efluentes e reflorestamento de áreas de entorno.
Tais ações estão inseridas em uma estratégia mais ampla de alinhamento às práticas de ESG (Environmental, Social and Governance), com metas de descarbonização em conformidade com os acordos climáticos internacionais e os Objetivos de Desenvolvimento Sustentável (ODS) da ONU (Diário do Rio, 2024; Notícias de Mineração Brasil, 2023).
Eficiência Energética e Autossuficiência
Outro diferencial da planta da Ternium em Santa Cruz é sua eficiência energética. Toda a energia elétrica consumida pela unidade é gerada internamente por meio de uma termelétrica própria, que opera a partir do aproveitamento dos gases e vapores residuais do processo siderúrgico, como o gás de alto-forno e gás LD (linz-donawitz).
Esse modelo de cogeração permite à empresa alcançar autossuficiência energética, reduzindo a demanda por energia externa e diminuindo os impactos ambientais associados à geração convencional de eletricidade (Ternium, 2024).
Conclusão
As ações implementadas pela Ternium no parque industrial de Santa Cruz reforçam o posicionamento da empresa como referência em siderurgia sustentável na América Latina. O uso de tecnologias limpas, energia renovável e economia circular representam passos concretos na transição para um modelo industrial mais verde, eficiente e alinhado aos desafios climáticos do século XXI.
Referências
- Brazil Journal. (2023). Ternium e o biometano: rumo ao aço verde. Disponível em: https://braziljournal.com
- Diário do Rio. (2024). Ternium anuncia R$ 650 milhões em investimentos ambientais no RJ. Disponível em: https://diariodorio.com
- Estadão. (2023). Uso de sucata metálica cresce na indústria siderúrgica brasileira.
- Notícias de Mineração Brasil. (2023). Iniciativas sustentáveis da Ternium no Brasil. Disponível em: https://nmb.com.br
- Ternium Brasil. (2024). Relatório ESG e Sustentabilidade. Disponível em: https://br.ternium.com
- UOL Economia. (2023). Produção de aço com biometano avança no Rio de Janeiro.
Cogeração de Energia: A Termelétrica Integrada ao Processo Siderúrgico
Um dos pilares de eficiência e sustentabilidade da unidade industrial da Ternium em Santa Cruz (RJ) é sua termelétrica integrada, que transforma subprodutos do processo siderúrgico — como gases de alto-forno e vapores — em energia elétrica. Esse sistema de cogeração é fundamental para garantir a autossuficiência energética da planta, além de se configurar como uma estratégia ambientalmente responsável.
Aproveitamento de Subprodutos Energéticos
Durante a produção de aço, são gerados diversos gases residuais, como o gás de coque, gás de alto-forno e gás LD (linz-donawitz). Em vez de serem descartados ou queimados de forma ineficiente, esses subprodutos são canalizados para alimentar caldeiras e turbinas na termelétrica localizada no próprio parque industrial. Essa integração permite o aproveitamento máximo da energia térmica contida nos gases, gerando eletricidade de forma contínua e estável.
Capacidade Instalada e Autossuficiência
Com uma capacidade de geração de aproximadamente 250 MW, a termelétrica da Ternium em Santa Cruz é capaz de suprir integralmente a demanda interna da planta siderúrgica, com potencial de excedente. Esse volume de geração excede a necessidade elétrica da unidade, e, em cenários de pico, pode inclusive fornecer energia para a rede elétrica externa, dependendo das regulamentações e contratos vigentes com o sistema de distribuição (Ternium, 2024).
Impacto na Sustentabilidade
Ao utilizar subprodutos do próprio processo industrial como fonte energética, a Ternium reduz significativamente sua dependência de combustíveis fósseis externos, como carvão mineral ou gás natural. Esse modelo reduz as emissões de CO₂ associadas à geração elétrica convencional, e contribui diretamente para o cumprimento das metas da empresa em termos de governança ambiental e descarbonização.
Além disso, o sistema de cogeração contribui para o desempenho energético da planta, reduzindo custos operacionais e aumentando a eficiência térmica e elétrica da unidade, conforme apontado em relatórios da empresa e publicações especializadas no setor siderúrgico (Notícias de Mineração Brasil, 2023; br.ternium.com, 2024).
Considerações
A integração de uma termelétrica ao parque industrial da Ternium representa um modelo de excelência em uso racional de recursos energéticos. Tal sistema não apenas assegura a independência energética da planta, como também posiciona a unidade de Santa Cruz como uma referência de inovação tecnológica e sustentabilidade industrial no cenário siderúrgico latino-americano.
Referências
- Ternium Brasil. (2024). Relatório de Sustentabilidade e Eficiência Energética da Planta de Santa Cruz. Disponível em: https://br.ternium.com
- Notícias de Mineração Brasil. (2023). Energia e sustentabilidade no setor siderúrgico: o caso Ternium.
- Estadão. (2023). Autossuficiência energética e cogeração no setor industrial.
- UOL Economia. (2023). Aço verde e uso de subprodutos energéticos pela Ternium.
Nucor Corporation
A Nucor Corporation é uma das maiores siderúrgicas do mundo e ocupa posição de destaque no mercado norte-americano. Reconhecida por sua eficiência operacional, inovação tecnológica e compromisso com a sustentabilidade, a Nucor se destaca pelo uso de mini-mills e por sua estratégia de produção baseada na reciclagem de sucata metálica. Este artigo analisa sua trajetória histórica, modelo de negócio, iniciativas sustentáveis, inovações tecnológicas, expansão de mercado e impacto econômico e social.
1. Introdução A indústria siderúrgica mundial tem passado por profundas transformações, impulsionadas por exigências ambientais, avanços tecnológicos e pressões econômicas. Nesse contexto, a Nucor Corporation desponta como um caso exemplar de adaptação e liderança. Fundada em 1940, a Nucor evoluiu de uma pequena fabricante de arames para uma gigante global da siderurgia.
2. História e Modelo de Negócio Inicialmente dedicada à produção de arames, a Nucor passou por diversas transformações até se consolidar como a maior produtora de aço dos Estados Unidos. A partir da década de 1960, a empresa adotou o modelo de mini-mills, pequenas usinas que utilizam fornos elétricos para fundir sucata metálica, substituindo os tradicionais altos-fornos baseados em minério de ferro e coque.
3. Operações e Produção As mini-mills da Nucor são altamente eficientes, com menor custo operacional e menor impacto ambiental. A empresa produz uma ampla variedade de produtos siderúrgicos, como vergalhões, placas de aço, arames, produtos estruturais e aço inoxidável, atendendo a setores como construção civil, infraestrutura, energia, automotivo e maquinário industrial.
4. Sustentabilidade A sustentabilidade é um dos pilares estratégicos da Nucor. A empresa investe fortemente em energia renovável, reciclagem de sucata e tecnologias de baixo carbono. Aproximadamente 70% de sua produção é baseada em sucata reciclada, o que contribui para uma emissão de CO₂ significativamente inferior à média global da indústria do aço (World Steel Association, 2023).
5. Inovação Tecnológica A Nucor é reconhecida por sua cultura de inovação e melhoria contínua. Seu investimento em tecnologias como fornos elétricos de arco (EAF), automação de processos e digitalização industrial tem contribuído para a otimização da produção e redução de custos. Essa eficiência operacional é um diferencial competitivo frente a outras siderúrgicas tradicionais.
6. Posição no Mercado Global A Nucor ocupa o primeiro lugar na produção de aço nos Estados Unidos e figura entre as dez maiores produtoras mundiais. Com dezenas de unidades operacionais, a empresa produz anualmente mais de 20 milhões de toneladas de aço bruto (Statista, 2023).
7. Expansão e Aquisições A estratégia de crescimento da Nucor é baseada em aquisições de empresas complementares e expansão de capacidade instalada. A empresa ampliou suas operações para o México e Canadá, buscando mercados estratégicos para aumentar sua presença internacional.
8. Impacto Econômico e Social A Nucor emprega mais de 25.000 trabalhadores e é reconhecida por sua cultura corporativa baseada em meritocracia, segurança e inclusão. A empresa também contribui significativamente para a economia norte-americana, sendo fornecedora-chave em projetos de infraestrutura e desenvolvimento industrial.
9. Resultados Financeiros Com lucros robustos e crescimento consistente, a Nucor tem mantido uma posição sólida no mercado. Seu modelo baseado em custo reduzido, eficiência energética e reciclagem confere à empresa resiliência frente às oscilações do setor siderúrgico.
Conclusão A Nucor Corporation representa um paradigma de eficiência, inovação e responsabilidade ambiental na indústria siderúrgica. Com um modelo de negócio baseado em mini-mills, reciclagem de sucata e uso intensivo de tecnologias limpas, a empresa não apenas assegura sua competitividade, mas também contribui para a transformação sustentável do setor.
Referências
- World Steel Association. (2023). Steel Statistical Yearbook.
- Statista. (2023). Leading steel producers worldwide based on production volume.
- Nucor Corporation. (2023). Sustainability Report. Disponível em: https://www.nucor.com
- American Iron and Steel Institute. (2022). Sustainability Indicators in Steel Manufacturing.
- U.S. Energy Information Administration. (2023). Industrial Energy Use and Efficiency in the Steel Sector.
A ArcelorMittal é uma das maiores empresas siderúrgicas globais, destacando-se por sua vasta capacidade de produção, presença internacional e compromisso com a sustentabilidade. Este artigo examina a trajetória histórica da empresa, suas operações, iniciativas de sustentabilidade e desafios enfrentados.
1. História e Formação
A ArcelorMittal foi estabelecida em 2006 pela fusão da Arcelor e da Mittal Steel, criando a maior produtora de aço mundial na época . A Arcelor surgiu em 2002, resultado da união de siderúrgicas europeias como Usinor, Arbed e Aceralia. Por outro lado, a Mittal Steel, fundada por Lakshmi Mittal, expandiu-se globalmente desde os anos 1970, consolidando-se como uma potência no setor .
2. Operações e Produção
A empresa produz uma ampla gama de produtos siderúrgicos, incluindo aços planos, longos e inoxidáveis, atendendo setores como construção civil, automotivo e energia. Em 2023, a capacidade de produção de aço bruto da ArcelorMittal foi de aproximadamente 81 milhões de toneladas .Home Page | ArcelorMittal
3. Presença Global
Com operações em mais de 60 países, a ArcelorMittal possui instalações significativas na América do Norte, Europa, América do Sul, África e Ásia. Na América do Norte, destaca-se a planta em Dofasco, Canadá, enquanto na Europa, possui operações em países como França e Bélgica. No Brasil, mantém instalações em Itaúna e outras localidades .
4. Sustentabilidade e Inovação
Comprometida com a redução de emissões de carbono, a ArcelorMittal almeja alcançar a neutralidade de carbono até 2050 e reduzir em 30% suas emissões na Europa até 2030 . Entre as iniciativas, destaca-se o projeto em Hamburgo, Alemanha, que utiliza hidrogênio na produção de aço , e a planta “Steelanol” em Gent, Bélgica, que transforma CO₂ capturado em bioetanol .Home Page | ArcelorMittal
5. Principais Projetos de Sustentabilidade
- Projeto de Hidrogênio Verde (Hamburgo): Implementação de tecnologia para reduzir minério de ferro utilizando hidrogênio, visando produção de aço com zero emissões de carbono .
- Captura de Carbono (Gent): Projeto pioneiro que converte CO₂ capturado em monóxido de carbono para uso na produção de aço e produtos químicos .Home Page | ArcelorMittal
- Transição para Produção de Aço Verde (Canadá): Conversão de operações para eliminar o uso de carvão, reduzindo emissões de carbono em 60% até 2028 .ArcelorMittal Dofasco
6. Resultados Financeiros
A ArcelorMittal mantém desempenho financeiro sólido, com vendas de US$ 34,0 bilhões e embarques de aço de 43,8 milhões de toneladas no primeiro semestre de 2015 .SEC
7. Desafios e Críticas
A empresa enfrenta desafios relacionados à concorrência global e à necessidade de investimentos significativos em tecnologias sustentáveis. Recentemente, adiou planos de transição para aço verde, citando falta de apoio político adequado da União Europeia .MarketWatch
Conclusão
A ArcelorMittal destaca-se como líder no setor siderúrgico, combinando vasta capacidade de produção com iniciativas inovadoras em sustentabilidade. Apesar dos desafios, seu compromisso com a redução de emissões e a transição para práticas mais ecológicas posiciona a empresa na vanguarda da indústria global de aço.
O Projeto H2 Green Steel e o Papel do Banco Europeu de Investimentos na Descarbonização da Indústria Siderúrgica
O setor siderúrgico é um dos maiores emissores de dióxido de carbono (CO₂) globalmente. Nesse contexto, o projeto H2 Green Steel surge como uma iniciativa inovadora de produção de aço utilizando hidrogênio verde em substituição ao carvão, visando a neutralidade climática. Este artigo discute os objetivos, impactos e desafios do projeto, bem como o papel estratégico do Banco Europeu de Investimentos (BEI) no financiamento de tecnologias de baixo carbono.
Palavras-chave: hidrogênio verde, aço sustentável, descarbonização, BEI, H2 Green Steel, energia renovável.
1. Introdução
A indústria siderúrgica responde por aproximadamente 7 a 9% das emissões globais de CO₂, sendo essencial a busca por soluções tecnológicas sustentáveis para alcançar as metas climáticas do Acordo de Paris e os compromissos da União Europeia (WORLD STEEL ASSOCIATION, 2023). O projeto H2 Green Steel, sediado na Suécia, propõe a produção de aço a partir do uso de hidrogênio verde como agente redutor do minério de ferro, em substituição ao carvão (H2 GREEN STEEL, 2023). Trata-se de uma inovação disruptiva com potencial para reduzir em até 95% as emissões de carbono associadas ao setor (EUROPEAN INVESTMENT BANK, 2023).
2. Objetivos e Características do Projeto
O projeto tem como objetivo implementar uma planta industrial com capacidade anual de produção de 5 milhões de toneladas de aço verde, com início de operação previsto para 2025 (H2 GREEN STEEL, 2023). A tecnologia empregada utiliza hidrogênio produzido por eletrólise, alimentada por fontes renováveis de energia, substituindo o coque nos altos-fornos tradicionais. O subproduto da reação, diferentemente do CO₂, é vapor d’água, tornando o processo ambientalmente limpo.
3. O Papel do Banco Europeu de Investimentos (BEI)
O BEI desempenha papel fundamental no financiamento de tecnologias sustentáveis na Europa. Alinhado com o Green Deal Europeu, o banco apoia projetos que contribuem para a neutralidade de carbono até 2050 (EUROPEAN COMMISSION, 2020). No caso do H2 Green Steel, o BEI disponibilizou recursos financeiros por meio de empréstimos verdes, permitindo a viabilidade econômica da infraestrutura de produção de hidrogênio e da planta siderúrgica (EUROPEAN INVESTMENT BANK, 2023).
Segundo o BEI, trata-se de um exemplo emblemático de transição industrial compatível com os princípios de sustentabilidade, inovação tecnológica e segurança energética (EUROPEAN INVESTMENT BANK, 2024).
4. Impacto Climático
Estudos indicam que a produção tradicional de aço pode emitir mais de 1,8 tonelada de CO₂ por tonelada de aço produzida (IEA, 2022). A substituição por hidrogênio verde poderá reduzir essas emissões em até 95%, dependendo da eficiência do sistema de eletrólise e da matriz energética utilizada. O H2 Green Steel projeta ser uma das plantas mais limpas do mundo, e se bem-sucedido, estabelecerá um novo paradigma para a produção industrial (H2 GREEN STEEL, 2023).
5. Localização e Infraestrutura Energética
A instalação da planta em Boden, próxima a Luleå, no norte da Suécia, foi estratégica. A região dispõe de abundantes fontes de energia renovável, sobretudo hídrica e eólica, além de uma rede elétrica robusta e estável (SWEDISH ENERGY AGENCY, 2023). Isso garante o fornecimento contínuo de eletricidade limpa para os processos eletroquímicos de geração de hidrogênio.
6. Investimentos e Financiamento
O H2 Green Steel já arrecadou mais de € 6 bilhões em financiamento, provenientes de investidores institucionais, fundos de sustentabilidade, bancos multilaterais e iniciativas privadas como a Breakthrough Energy Ventures (H2 GREEN STEEL, 2023). O BEI é um dos principais financiadores públicos do projeto, sendo responsável por aportes estratégicos voltados à infraestrutura de hidrogênio e à eletrificação dos processos industriais.
7. Impactos Econômicos e Sociais
O projeto prevê a criação de aproximadamente 1.500 empregos diretos e mais de 10 mil empregos indiretos, especialmente nas cadeias de fornecimento de equipamentos, construção e logística (H2 GREEN STEEL, 2023). A planta contribuirá significativamente para o desenvolvimento socioeconômico da região de Norrbotten, além de fomentar uma nova cadeia de valor associada à economia do hidrogênio.
8. Parcerias e Inovação Tecnológica
Além do suporte financeiro, o H2 Green Steel conta com parcerias tecnológicas para o desenvolvimento de eletrolisadores de larga escala e sistemas inteligentes de gestão energética. Empresas como a ABB, Siemens e produtores de eletrólise alcalina e PEM estão envolvidas no projeto (H2 GREEN STEEL, 2023). Essas alianças asseguram a robustez tecnológica e a escalabilidade do modelo industrial proposto.
9. Perspectivas Futuras
O sucesso do H2 Green Steel pode catalisar uma transformação global no setor siderúrgico, estimulando projetos semelhantes em outras regiões com acesso a energia renovável. Contudo, o projeto enfrenta desafios técnicos, como o custo elevado do hidrogênio verde e a necessidade de ampliar a capacidade de produção eletrolítica (IEA, 2022).
10. Conclusão
O projeto H2 Green Steel representa uma das mais ambiciosas iniciativas de descarbonização da indústria pesada no cenário europeu. Com o suporte do Banco Europeu de Investimentos e uma sólida base tecnológica, a planta sueca tem potencial para se tornar uma referência mundial em produção de aço sustentável. O sucesso do projeto dependerá de avanços técnicos, estabilidade regulatória e ampliação dos mercados de hidrogênio verde.
Referências
- EUROPEAN COMMISSION. A European Green Deal. 2020. Disponível em: https://commission.europa.eu/strategy-and-policy/priorities-2019-2024/european-green-deal_en. Acesso em: 08 abr. 2025.
- EUROPEAN INVESTMENT BANK. EIB supports H2 Green Steel with financing for Europe’s first large-scale green steel plant. 2023. Disponível em: https://www.eib.org/en/press/all/2023-062-eib-supports-h2-green-steel. Acesso em: 08 abr. 2025.
- H2 GREEN STEEL. H2 Green Steel Project Overview. 2023. Disponível em: https://www.h2greensteel.com/. Acesso em: 08 abr. 2025.
- IEA – INTERNATIONAL ENERGY AGENCY. Iron and Steel Technology Roadmap. 2022. Disponível em: https://www.iea.org/reports/iron-and-steel-technology-roadmap. Acesso em: 08 abr. 2025.
- SWEDISH ENERGY AGENCY. Renewable energy in Sweden. 2023. Disponível em: https://www.energimyndigheten.se/en/. Acesso em: 08 abr. 2025.
- WORLD STEEL ASSOCIATION. Steel’s contribution to a low carbon future. 2023. Disponível em: https://worldsteel.org. Acesso em: 08 abr. 2025.
O Forno Elétrico a Arco: Inovação, Sustentabilidade e Avanço Tecnológico na Indústria Siderúrgica
O forno elétrico a arco (FEA) é uma das tecnologias mais relevantes da indústria siderúrgica contemporânea. Desde sua concepção inicial no início do século XX por Paul Héroult, essa tecnologia passou por diversas transformações, consolidando-se como uma solução eficiente, flexível e ambientalmente mais responsável para a produção de aço.
1. Histórico e Desenvolvimento
O forno elétrico a arco teve seus primeiros conceitos formulados no início do século XIX, com o crescimento da aplicação da eletricidade nos processos industriais. Em 1909, o engenheiro francês Paul Héroult desenvolveu o primeiro modelo funcional de forno elétrico a arco, baseado na criação de um arco elétrico entre eletrodos de carbono, capaz de gerar calor suficiente para fundir metais como o ferro (Gordon, 1996).
O design de Héroult representou uma alternativa ao modelo dominante dos altos-fornos, sendo mais compacto, eficiente e com menor custo operacional. Esse forno passou a ser utilizado especialmente em mini-mills, que utilizam sucata metálica como principal insumo.
2. Características dos FEA Modernos
2.1 Eficiência Energética
Os fornos modernos têm capacidade de controlar com alta precisão o fornecimento de energia elétrica, permitindo otimização da fusão com menor desperdício de energia. Essa eficiência se traduz em redução de custos e emissões (Worrell & Reuter, 2014).
2.2 Sustentabilidade Ambiental
Ao utilizar ferro-velho como principal matéria-prima, o FEA reduz significativamente o consumo de recursos naturais e as emissões de CO₂. Ademais, tecnologias emergentes como a injeção de hidrogênio e sistemas de captura de carbono estão sendo integradas a esses fornos, como nas iniciativas HYBRIT (SSAB, 2021) e da ArcelorMittal em Ghent.
2.3 Versatilidade
Os FEA permitem a produção de diversos tipos de aço, como o carbono e inoxidável, dependendo da composição da carga e da temperatura, sendo ideais para demandas flexíveis do mercado.
2.4 Automacao e Controle Avançado
Os sistemas modernos incorporam sensores, controle em tempo real, algoritmos de inteligência artificial e automação para otimizar a qualidade e o rendimento do processo de produção (SMS Group, 2022).
3. Avanços Tecnológicos Recentes
3.1 Injeção de Hidrogênio
A utilização de hidrogênio verde como redutor no processo de fusão é uma das inovações mais promissoras. O projeto HYBRIT (SSAB, Vattenfall e LKAB) exemplifica o potencial dessa tecnologia na descarbonização da siderurgia (SSAB, 2021).
3.2 Captura de Carbono (CCS)
Empresas como ArcelorMittal e voestalpine têm investido em sistemas de captura e armazenamento de carbono, reduzindo as emissões sem alterar significativamente a infraestrutura existente (IEA, 2020).
3.3 Fornos de Alta Eficiência
Fabricantes como SMS Group e Danieli desenvolvem fornos equipados com controle inteligente de energia e fusão, com foco em eficiência energética e sustentabilidade.
3.4 Uso de Matérias-Primas Secundárias
A Nucor (EUA) é líder no uso de ferro-velho em mini-mills com FEA, com elevado grau de sustentabilidade e baixo custo de produção (World Steel Association, 2023).
3.5 Integração com Energia Renovável
Empresas como Tata Steel e SSAB estão investindo em energia solar e eólica para alimentar seus fornos, reduzindo a pegada de carbono da produção siderúrgica (IEA, 2020).
4. Caso Danieli: Fornos de Alta Eficiência
A italiana Danieli é referência mundial em tecnologia para siderurgia. Seus FEA são projetados com foco em:
- Controle de energia otimizado;
- Redução de perdas térmicas;
- Sistemas CCS integrados;
- Injeção de oxigênio;
- Automatização com sensores inteligentes;
- Uso intensivo de ferro-velho;
- Integração com energia renovável.
Exemplos de aplicação incluem projetos com a Nucor (EUA), Tata Steel (India) e várias siderúrgicas europeias alinhadas ao Pacto Verde da União Europeia.
Conclusão
Mais de um século após sua invenção, o forno elétrico a arco continua sendo pilar da siderurgia moderna. A evolução para tecnologias mais limpas, eficientes e integradas à economia circular torna o FEA uma ferramenta indispensável para uma indústria de aço sustentável.
Referências
- Gordon, R. B. (1996). American Iron and Steel Technology. AISE.
- Worrell, E., & Reuter, M. A. (2014). Handbook of Recycling. Elsevier.
- SSAB. (2021). HYBRIT – Hydrogen Breakthrough Ironmaking Technology. Disponível em: https://www.ssab.com
- IEA. (2020). Iron and Steel Technology Roadmap. International Energy Agency.
- World Steel Association. (2023). Steel Statistical Yearbook. Disponível em: https://www.worldsteel.org
- SMS Group. (2022). Smart electric arc furnace solutions. Disponível em: https://www.sms-group.com
- Danieli. (2023). High-Efficiency EAF Technology. Disponível em: https://www.danieli.com
A Evolução e Inovação dos Fornos Elétricos a Arco na Indústria Siderúrgica Moderna
O forno elétrico a arco (FEA) constitui uma das principais tecnologias utilizadas na produção de aço no mundo contemporâneo, notadamente em instalações de mini-mills que se caracterizam por processos mais eficientes e sustentáveis. Este artigo analisa a origem histórica do FEA, sua evolução tecnológica e os avanços recentes, com ênfase em eficiência energética, sustentabilidade e automação industrial. Através do estudo de casos industriais e inovações como a injeção de hidrogênio e a integração com fontes renováveis, delineia-se o papel central do FEA na transição para uma siderurgia de baixo carbono.
Palavras-chave: forno elétrico a arco, produção de aço, sustentabilidade, eficiência energética, Danieli, inovação siderúrgica.
1. Introdução
Desde o início do século XX, os fornos elétricos a arco têm desempenhado papel crucial na transformação da indústria siderúrgica. Com a crescente demanda por métodos produtivos sustentáveis e eficientes, o FEA passou a representar uma alternativa viável aos altos-fornos convencionais, sobretudo devido à sua capacidade de utilizar sucata metálica como matéria-prima principal, reduzindo significativamente a pegada de carbono do setor.
2. Histórico do Forno Elétrico a Arco
2.1 Invenção e Primeiros Modelos
A concepção inicial do FEA remonta ao início do século XIX, em um contexto de avanços significativos no campo da eletricidade. Em 1909, o engenheiro francês Paul Héroult desenvolveu o primeiro modelo funcional de forno elétrico a arco para fundição de metais, empregando arcos elétricos gerados entre eletrodos de carbono para gerar o calor necessário à fusão do ferro (Wintz, 2007).
2.2 Consolidação Tecnológica
O desenvolvimento do forno de Héroult representou um marco importante, pois introduziu um método mais eficiente e controlado para a produção de aço, em contraste com os altos-fornos, que exigem grandes volumes de carvão e minério de ferro. O modelo de Héroult tornou-se a base para as evoluções subsequentes do FEA ao longo do século XX e XXI.
3. Características dos Fornos Elétricos a Arco Modernos
3.1 Eficiência Energética
Os FEA modernos apresentam notável eficiência energética, utilizando eletricidade para fundir ferro-velho com consumo otimizado de energia elétrica. Segundo o World Steel Association (2021), o processo EAF consome cerca de 50% menos energia do que os métodos tradicionais a carvão.
3.2 Sustentabilidade e Redução de Emissões
O uso predominante de sucata metálica como insumo primário reduz drasticamente a necessidade de extração mineral, contribuindo para menores emissões de CO₂. Quando aliado ao uso de energias renováveis, o FEA pode atingir padrões elevados de sustentabilidade (IEA, 2022).
3.3 Versatilidade e Controle de Processo
A possibilidade de ajustar a composição química do aço durante o processo torna o FEA ideal para a produção de diferentes ligas, como aços inoxidáveis e especiais. A incorporação de tecnologias de controle computadorizado e sensores inteligentes permite precisão térmica e composição química ideal em tempo real.
4. Inovações Recentes em Fornos Elétricos a Arco
4.1 Injeção de Hidrogênio Verde
Projetos como o HYBRIT (Hydrogen Breakthrough Ironmaking Technology), conduzido por SSAB, LKAB e Vattenfall, na Suécia, propõem substituir o uso de carvão pelo hidrogênio verde. A reação do hidrogênio com o minério de ferro gera vapor d’água em vez de CO₂ (SSAB, 2022).
4.2 Tecnologias de Captura de Carbono (CCS)
Empresas como ArcelorMittal e voestalpine estão incorporando tecnologias de captura e armazenamento de carbono em seus fornos elétricos. A planta de Ghent, na Bélgica, é exemplo de aplicação industrial desta inovação, permitindo a redução direta das emissões no processo (ArcelorMittal, 2021).
4.3 Fornos de Alta Eficiência (High-Efficiency EAFs)
Fabricantes como SMS Group e Danieli lideram o desenvolvimento de fornos com controle avançado de temperatura, consumo de energia e composição do aço. Tais sistemas otimizam o processo de fusão e elevam a qualidade do produto final.
5. Caso Danieli: Excelência em Tecnologia de Fornos Elétricos
5.1 Histórico e Localização
A Danieli, fundada na Itália, é um dos principais fabricantes mundiais de fornos e soluções para a indústria metalúrgica. Sua sede está localizada em Buttrio, Friuli Venezia Giulia.
5.2 Características dos Fornos Danieli
- Eficiência energética otimizada: com perdas térmicas reduzidas e controle inteligente de energia.
- Redução de emissões: com integração de CCS e maior uso de materiais reciclados.
- Automação e sensores: para monitoramento em tempo real da fusão e ajuste automático da produção.
- Tecnologia de injeção de oxigênio: que acelera o processo e melhora a qualidade do aço.
- Integração com energia renovável: fornecimento híbrido ou totalmente limpo de energia elétrica.
5.3 Casos de Aplicação
- Nucor (EUA): mini-mills com uso extensivo de sucata metálica e fornos Danieli de última geração.
- Tata Steel (Índia): uso da tecnologia Danieli para maior eficiência energética.
- Siderúrgicas europeias: alinhadas com as metas de descarbonização da União Europeia até 2050.
6. Impacto Industrial e Perspectivas Futuras
O forno elétrico a arco transformou-se em um elemento essencial na modernização da siderurgia. Sua adaptabilidade ao uso de sucata e integração com tecnologias limpas tornam-no vital para as metas globais de redução de carbono. A tendência aponta para um futuro com fornos altamente automatizados, integrados a hidrogênio verde e operando com eletricidade proveniente de fontes renováveis.
7. Conclusão
Desde sua invenção por Paul Héroult em 1909, o forno elétrico a arco passou por uma trajetória evolutiva notável. Hoje, ele não apenas representa uma solução industrial eficiente, mas também um pilar na transição para uma economia de baixo carbono. Com inovações em curso como injeção de hidrogênio, captura de carbono e automação inteligente, o FEA consolida-se como tecnologia central na siderurgia do futuro.
Referências
- ArcelorMittal. (2021). Carbon capture technology at Ghent plant. Recuperado de: https://corporate.arcelormittal.com
- IEA – International Energy Agency. (2022). Iron and Steel Technology Roadmap. Paris: IEA Publications.
- SSAB. (2022). HYBRIT – Towards Fossil-Free Steel. Recuperado de: https://www.ssab.com/company/sustainability/hybrit
- World Steel Association. (2021). Steel Statistical Yearbook 2021. Bruxelas: World Steel Association.
- Wintz, J. (2007). Paul Héroult and the development of the electric arc furnace. Journal of Metallurgy and Materials, 59(2), 112-118.
O forno elétrico a arco começou a ser projetado no início do século XIX tendo seu primeiro modelo desenvolvido por Paul Héroult em 1909, que hoje, mais de 100 anos depois, ainda permanece como base para o design de suas versões mais modernas.
O forno elétrico a arco (FEA) é um dos principais métodos de produção de aço no mundo moderno, especialmente em instalações de mini-mills, onde a produção é mais eficiente e sustentável, utilizando ferro-velho como principal matéria-prima. A história desse forno é bastante interessante e está intimamente ligada aos avanços tecnológicos no campo da eletricidade e da siderurgia.
História do Forno Elétrico a Arco
A origem do forno elétrico a arco remonta ao início do século XIX, quando a utilização de energia elétrica começou a se expandir em diversas áreas industriais. O conceito básico do forno elétrico a arco envolve a passagem de uma corrente elétrica através de um arco entre dois eletrodos, criando um calor intenso que é suficiente para derreter metais como o ferro.
Primeiros Passos e Desenvolvimento:
No final do século XIX e início do século XX, a eletricidade começou a ser utilizada em maior escala em processos industriais, e a necessidade de métodos mais eficientes de fusão de metais levou ao desenvolvimento de novos processos.
Paul Héroult, um engenheiro francês, é creditado com a invenção do forno elétrico a arco. Em 1909, Héroult desenvolveu o primeiro modelo de forno elétrico a arco como uma solução para a fusão de metais de maneira mais eficiente e controlada.
O design de Héroult aproveitava a eletricidade para gerar um arco elétrico intenso entre os eletrodos de carbono, proporcionando calor suficiente para fundir o minério de ferro e transformar em aço.
Esse conceito foi um avanço significativo na época, especialmente porque, antes disso, o método predominante de produção de aço envolvia altos-fornos, que eram grandes e mais caros de operar.
O Forno Elétrico a Arco Moderno
Mais de 100 anos depois, o conceito básico do forno elétrico a arco de Héroult ainda é a fundação para a versão moderna desse equipamento, embora tenha passado por muitos aperfeiçoamentos ao longo das décadas. Aqui estão algumas características chave dos fornos elétricos a arco modernos:
Eficiência Energética:
Os fornos elétricos a arco modernos têm eficiência energética superior, utilizando eletricidade para derreter ferro-velho e produzir aço, sendo mais eficientes em termos de consumo de energia do que os altos-fornos tradicionais.
Sustentabilidade:
O forno elétrico a arco tem a vantagem de ser mais sustentável. Em comparação com o processo de altos-fornos, ele emite menos CO₂, especialmente quando utiliza ferro-velho reciclado, o que reduz a necessidade de minério de ferro e carvão, duas matérias-primas muito poluentes.
Versatilidade:
O forno elétrico a arco pode ser ajustado para diferentes tipos de aço, podendo ser usado para a produção de aço carbono, aço inoxidável e outros tipos de ligas metálicas, dependendo da temperatura e da composição da carga.
Aprimoramentos Tecnológicos:
Com o tempo, os fornos passaram a incorporar tecnologias como controle computadorizado, monitoramento em tempo real da temperatura e da qualidade do aço, e a injeção de oxigênio para melhorar a eficiência da fusão e otimizar os custos de operação.
Impacto no Setor Siderúrgico
O forno elétrico a arco revolucionou a indústria do aço porque possibilitou uma produção mais flexível, econômica e sustentável. Ele permitiu a criação de mini-mills, plantas de produção de aço menores e mais econômicas que podem usar sucata de aço reciclada como matéria-prima, ao contrário dos grandes altos-fornos que exigem minério de ferro.
A mini-siderurgia com fornos elétricos a arco tornou-se popular especialmente nas últimas décadas, permitindo a produção de aço de forma mais limpa e com menores custos de operação, o que tem sido fundamental para a indústria de aço moderna.
Hoje, os fornos elétricos a arco são responsáveis por uma parte significativa da produção mundial de aço, especialmente em países como os Estados Unidos, Brasil, e Europa, onde siderúrgicas de médio porte têm grande importância no mercado.
O forno elétrico a arco é um exemplo notável de como uma inovação centenária ainda pode ser a base para tecnologias modernas. Embora o design original de Paul Héroult tenha sido desenvolvido em 1909, ele permanece o ponto de partida para a produção de aço de maneira mais sustentável e eficiente. O forno elétrico a arco continua sendo uma tecnologia chave para a indústria siderúrgica, oferecendo não apenas eficiência energética e redução de emissões de carbono, mas também maior flexibilidade e versatilidade na produção de aço.
O forno elétrico a arco (FEA) moderno mais avançado do mundo evoluiu significativamente ao longo dos anos, com inovações focadas em eficiência energética, sustentabilidade e redução de emissões de carbono. A indústria tem feito avanços para melhorar não apenas a qualidade do aço, mas também reduzir o impacto ambiental da produção.
Aqui estão alguns dos fornos elétricos a arco mais modernos e as inovações que os tornam os mais avançados do mundo:
- Forno Elétrico a Arco com Injeção de Hidrogênio (H2)
Uma das tecnologias mais inovadoras em fornos elétricos a arco modernos é a injeção de hidrogênio como parte do processo de fusão. Em vez de usar apenas eletricidade para gerar o arco, o hidrogênio é injetado para aumentar a eficiência do processo e reduzir ainda mais as emissões de carbono.
Exemplo: HYBRIT (Hydrogen Breakthrough Ironmaking Technology) – Desenvolvido pela SSAB, Vattenfall e LKAB na Suécia, o projeto HYBRIT visa substituir carvão por hidrogênio verde, utilizando energia renovável para gerar o hidrogênio. Embora a tecnologia ainda esteja em fase de desenvolvimento, ela representa um avanço significativo no uso de hidrogênio no setor de siderurgia.
Vantagens: O uso de hidrogênio pode reduzir drasticamente as emissões de CO₂, já que o hidrogênio, ao reagir com o minério de ferro, gera apenas vapor d’água como subproduto, em vez de CO₂.
- Forno Elétrico a Arco com CO2 e Captura de Carbono
O forno elétrico a arco também tem sido melhorado para incorporar tecnologias de captura de carbono, que podem capturar as emissões de CO₂ durante o processo de produção do aço. Essa inovação visa atender às exigências de redução das emissões industriais.
Exemplo: ArcelorMittal e voestalpine, duas das maiores siderúrgicas do mundo, têm investido fortemente em tecnologias de captura e armazenamento de carbono (CCS) em seus fornos elétricos a arco. A planta de produção de aço em Ghent, Bélgica, da ArcelorMittal, está implementando tecnologia de captura de carbono em seus fornos, que pode reduzir significativamente as emissões de CO₂.
Vantagens: A captura de carbono permite que as siderúrgicas limitem suas emissões sem ter que mudar radicalmente a estrutura de suas operações. Além disso, a captura de CO₂ também pode ser utilizada para armazenamento geológico ou para uso industrial em outras aplicações.
- Fornos Elétricos a Arco de Alta Eficiência (High-Efficiency EAFs)
Os fornos elétricos a arco mais modernos estão equipados com tecnologias de controle automatizado e monitoramento em tempo real, otimizando a temperatura, o controle de carga e a energia consumida para maximizar a eficiência do processo.
Exemplo: SMS Group e Danieli são dois dos principais fabricantes de fornos elétricos a arco de alta eficiência. Eles integram sistemas de controle avançado, que permitem ajustar o fluxo de eletricidade de forma precisa, reduzindo o desperdício de energia e aumentando a qualidade do aço produzido.
Vantagens: Esses fornos são mais rápidos e eficientes em termos de consumo de energia, oferecendo um controle preciso da fusão do metal. A redução de energia não apenas contribui para uma produção mais econômica, mas também para menores emissões de CO₂.
- Forno Elétrico a Arco com Uso de Ferro-Velho e Matérias-Primas Secundárias
Os fornos elétricos a arco modernos são projetados para trabalhar com uma maior proporção de ferro-velho e outras matérias-primas recicladas. Isso não apenas reduz a necessidade de minerais virgens, mas também melhora a eficiência ambiental da produção de aço.
Exemplo: Nucor, uma das maiores produtoras de aço dos Estados Unidos, é líder em mini-mills e utiliza fornos elétricos a arco para derreter sucata metálica (ferro-velho). O processo da Nucor é altamente eficiente, com a empresa sendo uma das mais sustentáveis na indústria do aço, devido ao alto uso de materiais reciclados.
Vantagens: Ao usar ferro-velho, o forno elétrico a arco evita o uso de minério de ferro e carvão, reduzindo significativamente as emissões de carbono e o impacto ambiental da produção de aço.
- Forno Elétrico a Arco com Integração de Energia Renovável
A integração de fontes de energia renovável nos fornos elétricos a arco está se tornando uma tendência crescente, já que muitas siderúrgicas estão buscando reduzir a dependência de fontes de energia fóssil.
Exemplo: Tata Steel e SSAB têm demonstrado interesse em integrar energia eólica e solar em seus processos de produção de aço, utilizando eletricidade renovável para alimentar seus fornos elétricos a arco. Isso ajuda a reduzir o impacto ambiental e melhorar a sustentabilidade de suas operações.
Vantagens: O uso de energias renováveis para alimentar fornos elétricos a arco pode reduzir as emissões de carbono associadas à produção de aço e tornar o processo de produção mais verde. Também ajuda a reduzir os custos com eletricidade, especialmente em regiões com abundância de energia solar ou eólica.
Principais Características dos Fornos Elétricos a Arco Modernos
Eficiência Energética: Uso otimizado de eletricidade, com controle preciso do processo de fusão.
Redução de Emissões: Uso de hidrogênio verde, captura de carbono e ferro-velho para reduzir as emissões de CO₂.
Integração com Fontes Renováveis: Adoção de energias renováveis para alimentar o processo, minimizando a dependência de fontes de energia poluentes.
Automação e Controle Avançado: Monitoramento em tempo real, automação e controle de temperatura e qualidade do aço produzido.
Sustentabilidade: Uso de materiais reciclados, como ferro-velho, e desenvolvimento de processos para minimizar o desperdício de recursos.
O forno elétrico a arco moderno evoluiu muito desde sua invenção no início do século XX. As inovações mais recentes estão focadas em tornar o processo de produção de aço mais eficiente e sustentável, incorporando tecnologias como hidrogênio verde, captura de carbono, integração com energia renovável e uso de ferro-velho. Estas tecnologias não só reduzem o impacto ambiental, mas também tornam a produção de aço mais econômica e flexível. O futuro da siderurgia depende cada vez mais da tecnologia limpa e da inovação sustentável, com o forno elétrico a arco desempenhando um papel central nesse processo.
Fornos Elétricos a Arco de Alta Eficiência (High-Efficiency EAFs) Danieli
Os Forno Elétrico a Arco de Alta Eficiência (High-Efficiency EAFs) da Danieli são uma das soluções mais avançadas na produção de aço utilizando tecnologia de forno elétrico. A Danieli é uma das principais empresas no fornecimento de equipamentos e soluções para a indústria siderúrgica, e seus fornos elétricos a arco são projetados para atender às crescentes demandas por eficiência energética, sustentabilidade e alta qualidade na produção de aço.
Características dos Fornos Elétricos a Arco de Alta Eficiência (High-Efficiency EAFs) Danieli
Tecnologia EAF Ultra-eficiente
Os fornos de alta eficiência da Danieli são projetados para maximizar o uso de energia e reduzir as perdas térmicas durante o processo de fusão do aço.
A tecnologia inclui um controle otimizado da energia, o que significa que menos eletricidade é desperdiçada, o que contribui para uma redução de custos operacionais e menor impacto ambiental.
Redução de Emissões
A eficiência energética aprimorada reduz o consumo de energia elétrica e, portanto, minimiza as emissões de CO₂ associadas ao processo de produção.
Além disso, a Danieli incorpora tecnologias de captura e armazenamento de carbono (CCS) nos seus fornos para minimizar as emissões atmosféricas durante a produção.
Sistema de Controle Inteligente
Os fornos de alta eficiência da Danieli são equipados com sistemas de automação e controle inteligentes, que permitem a otimização em tempo real dos processos de fusão.
Esse controle inteligente ajuda a monitorar a qualidade do aço, ajustar os parâmetros de operação e garantir a produção de aço de alta qualidade.
O uso de sensores avançados permite um controle preciso da temperatura e da composição química do aço, garantindo que o produto final atenda às especificações exatas.
Uso de Materiais Reciclados
Os fornos da Danieli são projetados para maximizar o uso de ferro-velho (sucata de aço) como matéria-prima. O uso de materiais reciclados é uma estratégia chave para reduzir a necessidade de minério de ferro e reduzir as emissões de carbono associadas ao processo de produção.
O ferro-velho derretido no forno a arco elétrico é geralmente proveniente de indústrias recicladoras ou de recuperação de materiais, o que contribui significativamente para a sustentabilidade do processo.
Tecnologia de Injeção de Oxigênio
Muitos dos fornos elétricos a arco da Danieli são equipados com sistemas de injeção de oxigênio para melhorar a eficiência do processo de fusão. A injeção de oxigênio aumenta a taxa de fusão do material, reduzindo o tempo de operação e melhorando a qualidade do aço.
A injeção de oxigênio também ajuda a controlar as impurezas no aço e pode ser usada para aquecimento adicional do processo de fusão.
Integração com Energia Renovável
Um aspecto fundamental dos fornos de alta eficiência da Danieli é a integração com fontes de energia renováveis, como energia solar e eólica, para alimentar o forno elétrico a arco.
A empresa tem trabalhado em parceria com diversas siderúrgicas para integrar fontes de energia limpa, o que permite uma produção de aço ainda mais sustentável e ecologicamente responsável.
Vantagens dos Fornos Elétricos a Arco de Alta Eficiência da Danieli
Eficiência Operacional
A principal vantagem dos fornos de alta eficiência da Danieli é a redução de custos operacionais, graças à maior eficiência energética e ao menor consumo de eletricidade.
Esses fornos permitem uma produção mais rápida e econômica, com menos desperdício de energia e recursos.
Sustentabilidade
Como a produção de aço é uma das principais fontes de emissões de CO₂, os fornos da Danieli são projetados para minimizar essas emissões ao integrar tecnologias de captura de carbono e ao maximizar o uso de materiais reciclados como ferro-velho.
Além disso, a integração com energia renovável ajuda a reduzir a dependência de fontes de energia fóssil.
Qualidade do Produto
A alta precisão nos controles de temperatura e composição química do aço permite a produção de aços de alta qualidade, que atendem às exigências de diversas indústrias como automotiva, construção e indústria pesada.
Flexibilidade e Escalabilidade
Os fornos da Danieli são projetados para serem flexíveis e escaláveis, o que permite que as siderúrgicas adaptem a produção conforme as mudanças na demanda ou no mercado.
O uso de diversos tipos de materiais reciclados como entrada também oferece uma flexibilidade adicional na operação do forno.
Exemplos de Projetos de Fornos Elétricos a Arco Danieli
Nucor (EUA)
A Nucor, uma das maiores siderúrgicas dos Estados Unidos, tem utilizado fornos de alta eficiência da Danieli em suas plantas de mini-mills, focando na produção de aço a partir de sucata metálica reciclada. A parceria com a Danieli tem ajudado a otimizar a produção, reduzir custos operacionais e melhorar a sustentabilidade.
Tata Steel (Índia)
A Tata Steel também é uma das empresas que adota os fornos elétricos a arco da Danieli. A empresa implementou a tecnologia para melhorar sua eficiência energética e reduzir as emissões de carbono em suas operações de produção de aço.
Siderúrgicas na Europa
Várias siderúrgicas na Europa têm investido em tecnologias de alta eficiência da Danieli, com o objetivo de reduzir a pegada de carbono e melhorar a sustentabilidade na produção de aço. Isso está alinhado com os compromissos ambientais da União Europeia para alcançar a neutralidade climática até 2050.
Os fornos elétricos a arco de alta eficiência da Danieli representam o estado da arte em tecnologia siderúrgica, focando em eficiência energética, sustentabilidade e qualidade de produção. A integração de tecnologias avançadas, como controle inteligente, injeção de oxigênio, e uso de energia renovável, torna esses fornos altamente competitivos e ambientalmente responsáveis. Eles são a escolha de siderúrgicas modernas que buscam reduzir custos operacionais e melhorar a sustentabilidade de suas operações, enquanto atendem à crescente demanda global por aço de alta qualidade.
A Danieli é uma empresa italiana de engenharia e fabricação de equipamentos para a indústria metalúrgica, especialmente no setor de siderurgia. A sede global da Danieli está localizada em Buttrio, uma cidade na região de Friuli Venezia Giulia, no nordeste da Itália.
Detalhes sobre a Danieli:
Sede Global: Buttrio, Itália (província de Udine, região de Friuli Venezia Giulia).
Fundação: A Danieli foi fundada em 1914 e, ao longo das décadas, tornou-se uma das principais empresas de tecnologia e engenharia no setor siderúrgico global.
Além de sua sede em Buttrio, a Danieli possui diversas filiais e instalações ao redor do mundo, incluindo:
Escritórios e fábricas na América do Norte, América Latina, Ásia e Europa, para apoiar suas operações globais e seus clientes em várias regiões.
Centros de Pesquisa e Desenvolvimento em várias localidades, com inovações contínuas em tecnologias para a indústria de aço e metais.
A empresa se destaca pela integração vertical, oferecendo soluções completas para plantas siderúrgicas, que vão desde equipamentos para produção de aço até consultoria técnica e serviços de automação e controle.
A Laminação na Indústria Siderúrgica: Fundamentos, Processos e Aplicações
A laminação é um processo de conformação mecânica amplamente utilizado na indústria siderúrgica para transformar blocos metálicos, como lingotes e placas, em produtos com geometrias definidas, como chapas, tiras, barras e fios. Este trabalho tem como objetivo apresentar os fundamentos do processo de laminação, suas principais modalidades (laminação a quente e a frio), configurações de equipamentos, vantagens e aplicações industriais. A análise também considera os avanços tecnológicos e os benefícios sustentáveis associados a esse processo metalúrgico.
Palavras-chave: laminação, conformação mecânica, aço, laminação a quente, laminação a frio, siderurgia.
1. Introdução
A laminação constitui um dos processos industriais mais relevantes no contexto da siderurgia moderna, sendo responsável pela transformação de produtos semiacabados em componentes com dimensões e propriedades específicas. Consiste na redução da espessura e modificação da seção transversal de materiais metálicos por meio da passagem entre cilindros rotativos, sob condições controladas de pressão e temperatura.
Segundo Callister & Rethwisch (2021), a laminação representa cerca de 90% dos processos de conformação utilizados na produção de metais. Sua versatilidade, eficiência produtiva e capacidade de melhorar as propriedades mecânicas dos materiais justificam sua ampla aplicação nas indústrias automotiva, da construção civil, de eletroeletrônicos e de máquinas.
2. Fundamentos do Processo de Laminação
O processo de laminação baseia-se na deformação plástica do material metálico, promovida por sua passagem entre dois ou mais cilindros que giram em sentidos opostos. A ação mecânica dos rolos gera compressão e cisalhamento, resultando em redução da espessura e aumento da largura do produto. Parâmetros como temperatura, velocidade de laminação, tipo de rolo e lubrificação influenciam diretamente na qualidade do produto final (Ghosh & Mallik, 2003).
3. Classificação da Laminação
3.1 Laminação a Quente
Na laminação a quente, o material é aquecido a temperaturas superiores à recristalização (geralmente acima de 1000 °C no caso do aço), o que facilita sua deformação. O processo é utilizado principalmente para grandes reduções de espessura e volumes elevados de produção.
Vantagens:
- Maior eficiência em grandes volumes.
- Menor força de laminação.
- Possibilidade de deformar grandes seções transversais.
Aplicações:
- Chapas grossas para construção civil.
- Barras e perfis estruturais.
- Placas para posterior laminação a frio.
3.2 Laminação a Frio
Neste processo, a deformação ocorre em temperatura ambiente, após o material ter passado pela laminação a quente. O objetivo é refinar a espessura, melhorar o acabamento superficial e aumentar propriedades mecânicas como resistência à tração e dureza.
Vantagens:
- Melhor precisão dimensional.
- Superfície mais lisa e homogênea.
- Maior resistência mecânica devido ao encruamento.
Aplicações:
- Tiras metálicas para indústria eletrônica.
- Chapas para carrocerias automotivas.
- Materiais de alta precisão para engenharia mecânica.
4. Processos e Configurações de Laminação
4.1 Tipos de Processos
- Laminação de Passagem Única: indicada para reduções significativas de espessura em uma única operação.
- Laminação de Passagens Múltiplas: o material é submetido a várias passagens até atingir as dimensões desejadas.
- Laminação Contínua: utiliza várias gaiolas em sequência para alta produtividade.
- Laminação em Reversão: os rolos invertem a direção de rotação, possibilitando múltiplas passagens em um único laminador.
4.2 Tipos de Laminadores
- Laminadores de Dois Rolos: configuração simples, ideal para laminação inicial de chapas e blocos.
- Laminadores de Quatro Rolos: permitem maior controle sobre a espessura do produto e menor deflexão dos rolos.
- Laminadores de Seis Rolos ou Mais: aplicados em laminação de tiras finas e metais especiais com alto grau de precisão.
5. Vantagens Técnicas e Econômicas da Laminação
A laminação oferece uma série de benefícios técnicos, econômicos e ambientais:
- Alta produtividade: ideal para operações em larga escala.
- Baixo custo relativo: comparada a outros processos de conformação, como forjamento.
- Melhoria das propriedades mecânicas: especialmente em processos a frio.
- Sustentabilidade: menor geração de resíduos e maior aproveitamento de material metálico.
De acordo com Totten (2007), a laminação contribui para a refinação da microestrutura do aço, promovendo melhores características de resistência, dureza e ductilidade.
6. Aplicações Industriais
A versatilidade da laminação permite sua aplicação em diversos setores da economia:
- Indústria automotiva: fabricação de painéis, reforços estruturais e componentes de suspensão.
- Construção civil: vigas, chapas e perfis metálicos para edificações e pontes.
- Eletroeletrônicos: folhas metálicas finas para dispositivos eletrônicos e baterias.
- Engenharia mecânica: componentes de máquinas, ferramentas e sistemas de transmissão.
7. Considerações
A laminação é um dos pilares da produção moderna de aço e metais em geral. Seus processos, equipamentos e tecnologias continuam evoluindo, contribuindo para a eficiência produtiva, redução de custos e sustentabilidade ambiental da indústria metalúrgica. A escolha entre laminação a quente ou a frio, bem como o tipo de laminador, depende das especificações do produto final e das características do material a ser conformado.
Referências Bibliográficas
- CALLISTER, W. D.; RETHWISCH, D. G. Fundamentos da Ciência e Engenharia de Materiais. 10. ed. Rio de Janeiro: LTC, 2021.
- GHOSH, A.; MALLIK, A. K. Manufacturing Science. 2nd ed. New Delhi: East-West Press, 2003.
- TOTTEN, G. E. Steel Heat Treatment: Metallurgy and Technologies. Boca Raton: CRC Press, 2007.
- LANGE, K. Handbook of Metal Forming. New York: McGraw-Hill, 1985.
- KALPAKJIAN, S.; SCHMID, S. R. Manufacturing Engineering and Technology. 7th ed. Boston: Pearson, 2014.
Mineralogia: Fundamentos, Fontes Bibliográficas e Recursos de Estudo
A mineralogia é o ramo da geociência que estuda os minerais em seus diversos aspectos, como estrutura, propriedades físicas e químicas, ocorrência, classificação e identificação. Este artigo apresenta uma introdução à mineralogia e recomenda uma bibliografia fundamental para estudantes, pesquisadores e profissionais da área. São incluídas obras clássicas e contemporâneas, bem como recursos digitais e periódicos científicos especializados.
1. Introdução
A mineralogia desempenha um papel fundamental na compreensão da composição da Terra e na exploração de recursos naturais. Minerais são os blocos estruturais das rochas e, consequentemente, da crosta terrestre, tendo aplicações em setores como geologia, engenharia, mineração, metalurgia, entre outros (KLEIN; DUTROW, 2007). O domínio dos conceitos mineralógicos é essencial para diversas áreas das ciências da Terra, sendo respaldado por uma sólida base teórica disponível em obras especializadas e atualizações constantes via periódicos científicos e bases de dados.
2. Obras Clássicas e Referenciais em Mineralogia
2.1 Manual of Mineral Science (ou Dana’s Manual of Mineralogy) – Cornelis Klein
Este manual é uma referência clássica na área, reconhecido por sua abordagem detalhada sobre identificação, estrutura e propriedades dos minerais. A obra integra fundamentos de cristalografia, química mineral e petrologia.
Referência:
KLEIN, C.; DUTROW, B. Manual of Mineral Science. 23rd ed. Hoboken: John Wiley & Sons, 2007.
2.2 Introduction to Mineralogy – William D. Nesse
Obra amplamente utilizada em cursos de graduação, oferece uma introdução clara à estrutura, química e identificação dos minerais, com exemplos práticos e excelente didática.
Referência:
NESSE, W. D. Introduction to Mineralogy. 2nd ed. Oxford: Oxford University Press, 2012.
2.3 Mineralogy: Principles and Applications – Harvey Blatt; Bruce C. Middleton
Com foco na aplicação da mineralogia em contextos geológicos, o livro apresenta os princípios fundamentais com exemplos aplicados, sendo útil para geocientistas atuantes.
Referência:
BLATT, H.; MIDDLETON, B. C. Mineralogy: Principles and Applications. New York: W. H. Freeman, 2005.
2.4 The Rock and Gem Book – DK
Embora de caráter não técnico, este material é altamente visual e acessível, ideal para iniciantes e interessados em gemologia e formação mineral.
Referência:
DK. The Rock and Gem Book: And Other Treasures of the Natural World. New York: DK Publishing, 2016.
2.5 Physical Geology: Earth Revealed – Charles C. Plummer; Diane H. Carlson
Focado em geologia física, inclui capítulos sobre mineralogia, oferecendo uma visão integrada dos processos geológicos que influenciam a formação e transformação dos minerais.
Referência:
PLUMMER, C. C.; CARLSON, D. H. Physical Geology: Earth Revealed. 9th ed. New York: McGraw-Hill, 2012.
2.6 Descriptive Mineralogy – Cornelis Klein
A obra apresenta uma descrição sistemática e detalhada de minerais, com tabelas, diagramas e critérios objetivos de identificação.
Referência:
KLEIN, C. Descriptive Mineralogy. New York: W. H. Freeman, 1985.
3. Bibliografia em Português
3.1 Mineralogia: Introdução ao Estudo dos Minerais – Roberto F. A. Pereira
Trata-se de uma introdução abrangente em língua portuguesa, abordando desde conceitos fundamentais até aspectos estruturais e aplicações geológicas.
Referência:
PEREIRA, R. F. A. Mineralogia: Introdução ao Estudo dos Minerais. São Paulo: Oficina de Textos, 2008.
3.2 Mineralogia: Fundamentos e Aplicações – Luís A. S. H. Oliveira
A obra explora fundamentos teóricos com enfoque em aplicações geológicas e tecnológicas da mineralogia, ideal para cursos superiores.
Referência:
OLIVEIRA, L. A. S. H. Mineralogia: Fundamentos e Aplicações. Belo Horizonte: Editora UFMG, 2014.
4. Periódicos Científicos Especializados
Para além dos livros, periódicos especializados oferecem atualizações sobre descobertas e avanços científicos:
- American Mineralogist: Publica pesquisas avançadas em mineralogia, cristalografia e geoquímica.
https://www.minsocam.org - Minerals (MDPI): Revista de acesso aberto com foco em aspectos fundamentais e aplicados da mineralogia.
https://www.mdpi.com/journal/minerals
5. Recursos Digitais e Bases de Dados
5.1 Mindat.org
Principal base de dados mineralógicos online, oferece descrições, fotos, ocorrências geográficas e dados cristalográficos.
https://www.mindat.org
5.2 Minerals.net
Portal educativo com guias para identificação de minerais, glossários, galerias e dados físicos.
https://www.minerals.net
5.3 Geology.com
Plataforma abrangente sobre geologia, com seções dedicadas à mineralogia e mapas geológicos.
https://www.geology.com
6. Conclusão
O estudo da mineralogia é essencial para a compreensão dos processos geológicos e para a aplicação técnica em setores estratégicos como mineração, engenharia e meio ambiente. A bibliografia apresentada neste artigo oferece uma base sólida para diferentes níveis de estudo, desde o introdutório até o avançado. A combinação de livros clássicos, publicações periódicas e bases de dados digitais proporciona uma abordagem integrada e atualizada da disciplina.
Da Mineralogia ao Aço: A Jornada dos Minerais até as Aplicações na Indústria Automobilística e Engenharia Civil
- Introdução A mineralogia, como ramo da geociência, tem papel essencial na compreensão dos materiais utilizados em diversos setores industriais. A indústria siderúrgica, por sua vez, depende diretamente de minerais como o minério de ferro, o carvão mineral e o calcário para a produção de aço, material de ampla aplicação na indústria automobilística e na engenharia civil. Este artigo tem como objetivo apresentar a relação entre a mineralogia e a produção de aço, abordando os processos de transformação mineralógica, as propriedades dos diferentes tipos de aço e suas aplicações tecnológicas, com ênfase em sustentabilidade e inovação.
- A Mineralogia e a Formação de Minerais Importantes para a Produção de Aço Os principais minerais utilizados na siderurgia são o minério de ferro, o carvão mineral (coque) e o calcário. O minério de ferro, composto majoritariamente por hematita (Fe2O3) e magnetita (Fe3O4), é obtido de jazidas geológicas através de processos de mineração e beneficiamento. O coque, derivado do carvão mineral, é essencial para fornecer energia e atuar como agente redutor nos altos-fornos. O calcário (CaCO3) atua como fundente, promovendo a remoção de impurezas e formação de escória.
- Do Minério ao Aço: Processos de Produção A transformação do minério em aço envolve diversas etapas. Inicialmente, o minério é fundido em altos-fornos, gerando ferro gusa. Em seguida, este passa por processos de refino em convertedores a oxigênio (LD) ou fornos elétricos a arco (EAF), removendo impurezas e ajustando a composição química do aço. A laminação é utilizada para transformar o aço líquido em produtos acabados como chapas, vigas e barras.
- Tipos de Aço e suas Propriedades Os principais tipos de aço são:
- Aço carbono: com baixo teor de elementos de liga, possui boa conformabilidade e é amplamente usado em estruturas.
- Aço inoxidável: adicionado de cromo, apresenta alta resistência à corrosão, ideal para ambientes agressivos.
- Aço de baixa e alta liga: com aditivos como manganês, níquel e molibdênio, oferece propriedades específicas como resistência ao desgaste e altas temperaturas.
- Aços na Indústria Automobilística O uso de aços de alta resistência permite reduzir o peso dos veículos, melhorar a eficiência energética e garantir maior segurança. Componentes como carrocerias, suspensões, rodas e sistemas estruturais utilizam aços com diferentes propriedades mecânicas. A inovação nos processos de estampagem e soldagem de aços avançados tem permitido projetos veiculares mais eficientes.
- Aços na Engenharia Civil Na construção civil, o aço é essencial em estruturas de concreto armado, armações e elementos de sustentação. Sua resistência mecânica e durabilidade tornam-no ideal para pontes, torres, arranha-céus e instalações industriais. A modernização das normas técnicas e o uso de BIM (Building Information Modeling) têm impulsionado a aplicação eficiente do aço.
- Sustentabilidade e Reciclagem de Aço O aço é 100% reciclável, o que o torna um dos materiais mais sustentáveis do planeta. A utilização de sucata como matéria-prima nos fornos elétricos reduz o consumo de energia e as emissões de CO2. Iniciativas como o uso de hidrogênio verde no processo de redução direta e tecnologias de captura e armazenamento de carbono estão em desenvolvimento para reduzir o impacto ambiental da siderurgia.
- Conclusão A trajetória dos minerais até sua aplicação como aço em setores fundamentais da sociedade demonstra a interdependência entre as ciências da Terra e a engenharia. A compreensão mineralógica é a base para o aproveitamento racional dos recursos naturais, enquanto os avanços tecnológicos na produção e uso do aço evidenciam sua relevância estratégica em uma sociedade industrial e cada vez mais voltada à sustentabilidade.
Referências
- Klein, C. & Dutrow, B. (2007). Manual of Mineral Science. Wiley.
- Nesse, W. D. (2012). Introduction to Mineralogy. Oxford University Press.
- Blatt, H., & Middleton, B. C. (2006). Mineralogy: Principles and Applications. Cambridge University Press.
- Pereira, R. F. A. (2010). Mineralogia: Introdução ao Estudo dos Minerais. Editora UFPR.
- Oliveira, L. A. S. H. (2018). Mineralogia: Fundamentos e Aplicações. Oficina de Textos.
- American Iron and Steel Institute (AISI). (2023). Steel Industry Sustainability Reports.
- World Steel Association (2023). World Steel in Figures.
- Mindat.org. Mineral Database. Acesso em: https://www.mindat.org
- Geology.com. Steel Resources. Acesso em: https://geology.com
Da Produção Global à Reciclagem: Panorama Atual da Indústria do Aço e suas Principais Aplicações
Resumo Este artigo apresenta um panorama atualizado da indústria siderúrgica mundial, com foco na produção global de aço, os principais produtores, os métodos de produção (primária e reciclada), e os setores que mais consomem este material. Particular atenção é dada à construção civil e à indústria de petróleo, onde o aço é empregado em larga escala.
1. Introdução A produção mundial de aço é um dos pilares da economia global, refletindo o nível de industrialização e desenvolvimento dos países. Em 2023, a produção global de aço foi estimada em cerca de 1,9 bilhão de toneladas (World Steel Association, 2024), envolvendo mais de 50 grandes siderúrgicas ao redor do globo.
2. Principais Produtores de Aço Entre os maiores produtores, destacam-se China Baowu Steel, ArcelorMittal, Nippon Steel, HBIS Group e POSCO. A China Baowu lidera o ranking com mais de 100 milhões de toneladas produzidas anualmente, seguida pela ArcelorMittal com cerca de 70 milhões de toneladas (Statista, 2024). A produção total das 50 maiores empresas ultrapassa 1 bilhão de toneladas anuais, com as siderúrgicas chinesas respondendo por mais da metade deste volume.
3. Produção Primária vs. Reciclagem A indústria do aço divide-se entre a produção primária, a partir de minério de ferro, e a produção secundária, por meio da reciclagem de sucata. Aproximadamente 30% a 40% do aço produzido globalmente é reciclado, utilizando fornos elétricos a arco (EAF). Este método reduz significativamente o consumo de energia e as emissões de CO₂ (World Steel Association, 2023). Ainda assim, cerca de 60% a 70% do aço é produzido via alto-forno, empregando minério de ferro, carvão e calcário.
4. Setores Consumidores de Aço
4.1 Construção Civil A construção civil é o principal setor consumidor de aço, representando mais de 50% da demanda global. O aço é essencial na armação de concreto, estruturas metálicas, dutos, telhados e fundações. A urbanização crescente e os investimentos em infraestrutura aumentam continuamente essa demanda (OECD, 2023).
4.2 Indústria Automobilística O setor automotivo consome entre 15% e 20% do aço mundial, empregando-o em carrocerias, suspensões, motores e estruturas de segurança. A busca por veículos mais leves e seguros tem impulsionado o uso de aços de alta resistência (WorldAutoSteel, 2023).
4.3 Indústria de Energia e Petróleo Na indústria de energia, o aço é empregado em dutos, torres, equipamentos e estruturas offshore. A demanda é elevada devido à necessidade de materiais duráveis e resistentes à corrosão e à pressão.
5. Plataformas de Petróleo e o Consumo de Aço
5.1 Plataformas Fixas Plataformas fixas consomem entre 30.000 e 50.000 toneladas de aço, necessárias para estruturas de apoio, pilares e fundações que resistem a condições marinhas extremas (DNV, 2022).
5.2 Plataformas Flutuantes (FPSOs e Semissubmersíveis) FPSOs e plataformas semissubmersíveis consomem de 10.000 a 30.000 toneladas de aço, variando conforme o projeto e a capacidade de produção.
5.3 Plataformas de Perfuração Estas estruturas utilizam entre 5.000 e 20.000 toneladas de aço, empregadas principalmente em sistemas de perfuração e estruturas de suporte.
5.4 Outros Componentes Aço também é essencial em dutos, sistemas de ancoragem, equipamentos de segurança e superestruturas das plataformas.
6. Conclusão A indústria siderúrgica global continua a desempenhar um papel central na infraestrutura moderna. Embora a reciclagem de aço esteja em crescimento, a produção primária ainda domina o setor. A construção civil lidera o consumo de aço, seguida por setores estratégicos como automobilístico e de energia. O uso intensivo de aço em plataformas de petróleo evidencia sua importância em ambientes extremos e tecnologicamente exigentes.
Referências
- World Steel Association. (2023). Steel Statistical Yearbook 2023. https://worldsteel.org
- World Steel Association. (2024). Top steel-producing companies 2023. https://worldsteel.org
- OECD. (2023). Steel Market Developments Q4 2023. https://www.oecd.org/industry/ind/steel.htm
- Statista. (2024). Leading steel producers worldwide as of 2023. https://www.statista.com
- DNV. (2022). Offshore standards and steel structure assessments. https://www.dnv.com
- WorldAutoSteel. (2023). Advanced High-Strength Steel for Automotive Applications. https://www.worldautosteel.org
Posts recentes:
- Tensões políticas, possest e alteridade
- Pentadialética e decadialética contemporânea
- O signo é a luz do ser refletida na linguagem
- Israel, Irã, Pérsia e Paraíso
- Ciência, Serpentes, Tentação e Cultura Pop
Links Externos:
A produção global de aço é dominada por um número significativo de siderúrgicas em todo o mundo. Em 2023, a produção global de aço foi estimada em cerca de 1,9 bilhão de toneladas. Isso inclui as produções de mais de 50 grandes siderúrgicas que operam globalmente.
As principais siderúrgicas, como ArcelorMittal, China Baowu Steel, Nippon Steel, HBIS Group e POSCO, são responsáveis por uma grande parte dessa produção. Por exemplo:
China Baowu Steel é a maior produtora de aço do mundo, com uma produção anual superior a 100 milhões de toneladas.
ArcelorMittal, a segunda maior, produz cerca de 70 milhões de toneladas anualmente.
Outras siderúrgicas, como Nippon Steel e HBIS Group, produzem entre 40 a 50 milhões de toneladas por ano.
Se somarmos a produção das mais de 50 maiores siderúrgicas globais, a produção total anual ultrapassa 1 bilhão de toneladas, com destaque para as siderúrgicas chinesas, que sozinhas representam uma grande parcela dessa produção devido à capacidade do setor industrial da China.
Portanto, mais de 1 bilhão de toneladas de aço é produzido anualmente pelas principais siderúrgicas globais, com a China respondendo por mais da metade dessa produção.
- A Maioria do Aço Vem de Reciclagem?
A produção de aço global é uma combinação de produção primária (a partir de minério de ferro) e reciclagem (a partir de sucata de aço). A reciclagem de aço tem se tornado cada vez mais significativa, especialmente porque o aço é 100% reciclável sem perder qualidade, e a reciclagem ajuda a reduzir o impacto ambiental.
Reciclagem de Aço: Aproximadamente 30% a 40% da produção global de aço vem da reciclagem de sucata de aço, ou seja, do uso de aço reciclado. Este processo é realizado principalmente em fornos elétricos a arco (EAF), que usam sucata de aço como principal matéria-prima, ao invés de minério de ferro. A reciclagem de aço é mais eficiente em termos energéticos e emite menos gases de efeito estufa do que a produção a partir de minério de ferro.
Produção Primária: O restante, cerca de 60% a 70% da produção global de aço, é gerado a partir de processos de produção primária, como o alto-forno, que usa minério de ferro, carvão (coque) e calcário para produzir ferro gusa, que depois é convertido em aço.
Portanto, embora a reciclagem de aço seja uma prática crescente e importante, a maior parte do aço ainda é produzida de forma primária, a partir de minério de ferro.
- A Maioria do Aço Vai para a Construção Civil?
Sim, a construção civil é, de longe, o maior setor consumidor de aço, representando uma grande parte da demanda global. O aço é utilizado em diversas aplicações estruturais, sendo essencial em projetos de infraestrutura e construção de edifícios. Entre as aplicações na construção civil, incluem-se:
Estruturas de Concreto Armado: O aço é amplamente utilizado nas armações de concreto para garantir resistência e estabilidade às construções.
Estruturas Metálicas: O aço também é usado em estruturas metálicas para edifícios, pontes, viadutos e outras infraestruturas de grande porte, devido à sua alta resistência e durabilidade.
Tubulações e Dutos: O aço é usado em sistemas de encanamentos e dutos para água, gás, e sistemas de ventilação.
Telhados e Fundações: Aços de alta resistência também são usados para estruturas de telhados, fundamentos e pilares.
A indústria da construção civil é responsável por mais de 50% da demanda global de aço. Esse consumo é impulsionado pela crescente urbanização e pelo aumento da necessidade de infraestrutura em países em desenvolvimento e em mercados maduros, como na construção de arranha-céus, estruturas de transporte (pontes, rodovias, ferrovias) e instalações industriais.
Outros Setores que Consomem Aço
Embora a construção civil seja o maior consumidor, o aço também é crucial em outras indústrias, como:
Indústria Automobilística: O aço é amplamente utilizado na fabricação de veículos, principalmente para carrocerias, componentes de suspensão, estruturas de segurança e sistemas de transmissão. A indústria automobilística consome cerca de 15% a 20% do aço globalmente.
Indústria de Energia e Petróleo: O aço é fundamental para a construção de dutos, gasodutos, torres de transmissão de energia e equipamentos petroquímicos. Essas indústrias também consomem uma quantidade significativa de aço, principalmente para garantir resistência à corrosão e suporte a altas pressões.
Indústria de Eletrodomésticos e Equipamentos: O aço é utilizado para a fabricação de eletrodomésticos, como geladeiras, máquinas de lavar, e equipamentos industriais, como máquinas e ferramentas.
Reciclagem: Aproximadamente 30% a 40% do aço global vem de reciclagem, mas a maior parte ainda é produzida de forma primária, a partir de minério de ferro.
Construção Civil: Mais de 50% do aço produzido globalmente vai para a construção civil, devido à alta demanda por infraestrutura, edificações e estruturas metálicas.
Portanto, enquanto a reciclagem de aço é um aspecto crescente e vital da indústria siderúrgica, o aço primário ainda domina, e a construção civil continua sendo o principal setor consumidor desse material essencial.
A quantidade de aço utilizada em plataformas de petróleo pode variar bastante dependendo do tipo e do tamanho da plataforma, bem como do projeto específico. No entanto, plataformas de petróleo, especialmente as plataformas fixas e flutuantes (FPSOs), fazem uso significativo de aço devido à necessidade de materiais resistentes à corrosão, à pressão e às condições ambientais extremas do mar.
Plataformas de Petróleo e o Consumo de Aço
- Plataformas Fixas
Plataformas fixas, que são construídas diretamente sobre o fundo marinho, exigem uma enorme quantidade de aço, principalmente nas suas estruturas de suporte. Estima-se que uma plataforma fixa de grande porte possa consumir entre 30.000 e 50.000 toneladas de aço ou mais, dependendo do tamanho e do tipo de plataforma. O aço é utilizado na construção de:
Estrutura de apoio: A base fixada no fundo marinho, que precisa ser extremamente forte para suportar as plataformas e resistir ao impacto de ondas e correntes marítimas.
Pilares e fundações: Aços de alta resistência são empregados na construção das fundações e pilares que sustentam toda a estrutura da plataforma.
- Plataformas Flutuantes (FPSOs e Semissubmersíveis)
As FPSOs (Floating Production Storage and Offloading units) e plataformas semissubmersíveis também fazem uso significativo de aço, embora o consumo de aço possa ser ligeiramente menor do que nas plataformas fixas devido à diferença nas estruturas e no tipo de flutuabilidade. Para plataformas flutuantes grandes, o consumo de aço pode chegar a 10.000 a 30.000 toneladas, dependendo da capacidade de produção e das características da plataforma. - Plataformas de Perfuracão
As plataformas de perfuração também fazem uso de grandes quantidades de aço, embora em menor escala que as plataformas de produção. Elas podem consumir de 5.000 a 20.000 toneladas de aço, com a maior parte sendo usada nas estruturas de suporte e no sistema de perfuração. - Outras Aplicações e Componentes
Além das grandes estruturas, outras partes da plataforma também exigem aço, incluindo:
Dutos e tubulações para o transporte de petróleo e gás.
Sistemas de ancoragem para plataformas flutuantes.
Equipamentos de segurança e sistemas de controle.
Armações e superestruturas da plataforma.
A quantidade de aço utilizado em plataformas de petróleo pode variar dependendo do tipo de plataforma, mas em geral, uma plataforma de petróleo de grande porte pode consumir entre 10.000 e 50.000 toneladas de aço, sendo que as plataformas fixas de grande porte tendem a exigir a maior quantidade de material devido à sua estrutura robusta necessária para resistir às condições extremas no fundo do mar. O aço é essencial em todas as fases de construção e operação das plataformas de petróleo, desde as fundações até os sistemas de perfuração e produção.